
3 of the Latest Hydroformed Components Hitting the Market
As we so often do, we like to focus on hydroformed components that are making waves in the modern world. From mountain bikes to car parts to aerospace design, hydroformed components and prod ...
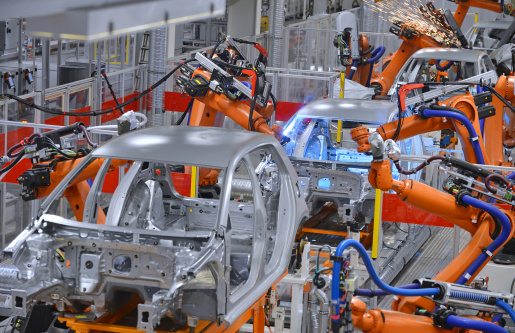
Hydroformed Components Make Trucks Stronger, Faster, and Better
We've talked in length before about how hydroformed components used in the automobile industry have helped to change the entire process. Every few months or so, we like to update our reader ...

In House Finite Element Analysis Capabilities
Finite Element Analysis (FEA) is an engineering simulation discipline that has its roots in the aerospace industry, during the 1950’s. Since that time the discipline has ‘come into its own,’ spurred ...