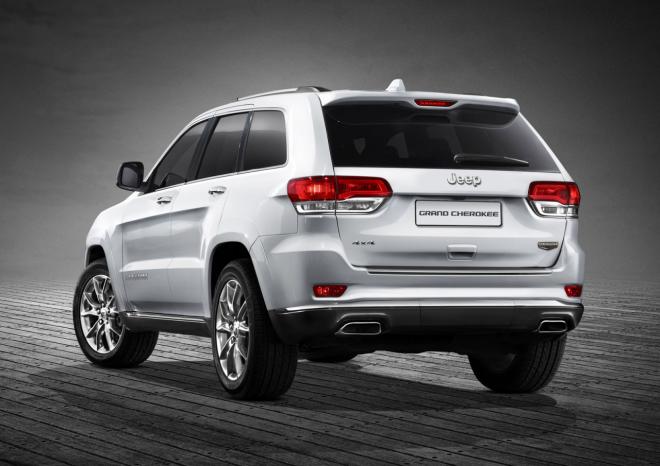
Vehicles Using Hydroformed Components
Hydroformed components play a major role in the design and production of automobiles. From headliners to hood seals and headlights, sheet and tube hydroforming are used in the manufacturing process fo ...

Hydroformed Components Revive Classic Cars
Hydroformed automotive parts are showing up on a lot of new car models - the Ford Fusion, the 2014 Chevrolet Corvette and the Chevrolet Silverado, for example - but new cars are not the only vehicles ...

Hydroforming Increases Automobile Safety
You might not know it, but you may have hydroforming to thank for the fact that you weren't injured in your last fender-bender. What is hydroforming? Generally speaking, hydroforming is a technique ...
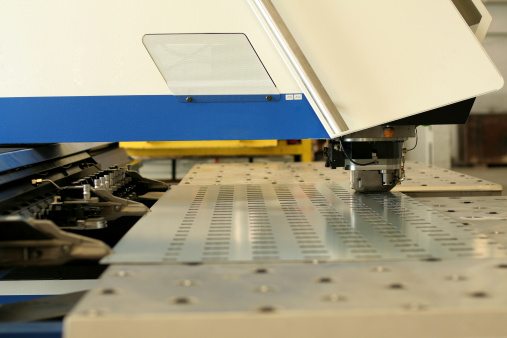
Advancements in Metal Stamping
Hard on the heels of the announcement that General Motors has opened a new metal stamping plant in Arlington, Texas, comes further information regarding how the opening of this new plant has impacted ...