
What Is Hydroforming Used To Create?
When some people hear the word “hydroforming”, they immediately have questions about the definition of hydroforming. They want to know the definition of hydroforming, they want to know what the hydrof …

Manufacturing Hydroformed Tubes
Tube hydroforming plays a critical role in manufacturing. Before the presence of hydroforming, there was no way to create solid and durable tubes in complex shapes that could withstand the test of tim …

Get the Facts About Tube Hydroforming
Get the Facts About Tube Hydroforming
There are two common types of hydroforming, tube hydroforming, and sheet hydroforming. But first, what is ‘hydroforming?’ It’s the process by which metals like …

What Is Hydroforming
The way of shaping various metals such as stainless steel, aluminum, brass, and other metals into weighted pieces that are durable and solid is known as hydroforming. Generally, hydroforming is used i …
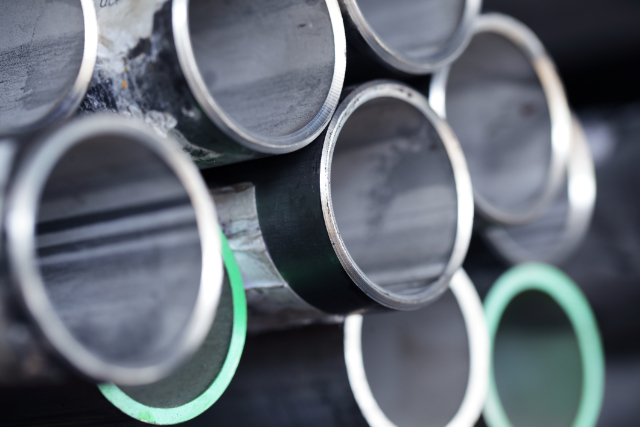
How Hydroforming Works and What It Is
How hydroforming works and what it is. Hydroforming is a cost-efficient way of transforming and shaping ductile metals (like aluminum and stainless steel) into lightweight, sturdy pieces. It uses flui …

What Is Hydroforming And How Can It Help You?
When discussing hydroforming with some who has never heard of the process, the obvious question that will arise is: what is hydroforming?
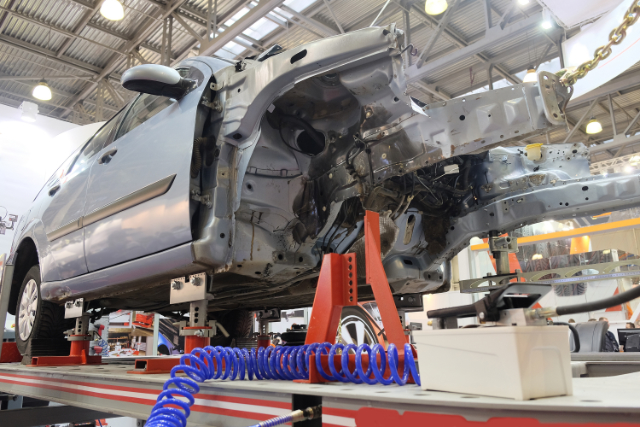
Why Is Tube Hydroforming A Preferred Solution?
The technique that is used to create hydroformed metal bellows
that are used in multiple industries is known as tube hydroforming. Tube
hydroforming is used in a variety of industries that produce par …
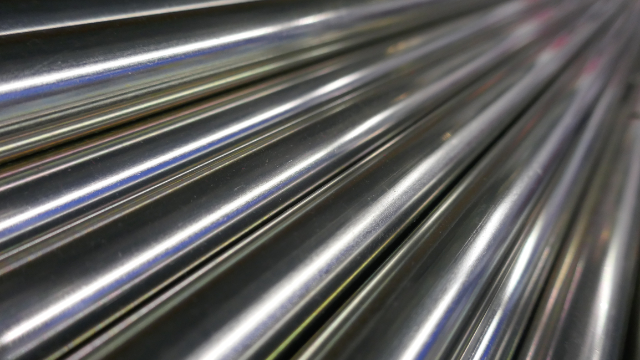
What is Tube Hydroforming? The History and Background Explained
First developed in the late 1940s and early 1950s, tube
hydroforming is the process by which pressurized fluid, either hydraulic fluid
or water, is used to expand and shape metal tubes into the contou …

Tube Hydroforming Will Continue To Have A Place In The Industry
While it may still be seen as one of the newer methods in the industry, especially when compared to the conventional or traditional stamping processes, tube hydroforming continues to have a large impa …

What Is Tube Hydroforming: Improving Auto Safety
Most individuals are trying to cut costs and save money. One way is to purchase a fuel-efficient car. But most of those cars are compact cars and on the road with larger vehicles, safety can be a conc …