Hydroforming Rides New Wave of Interest
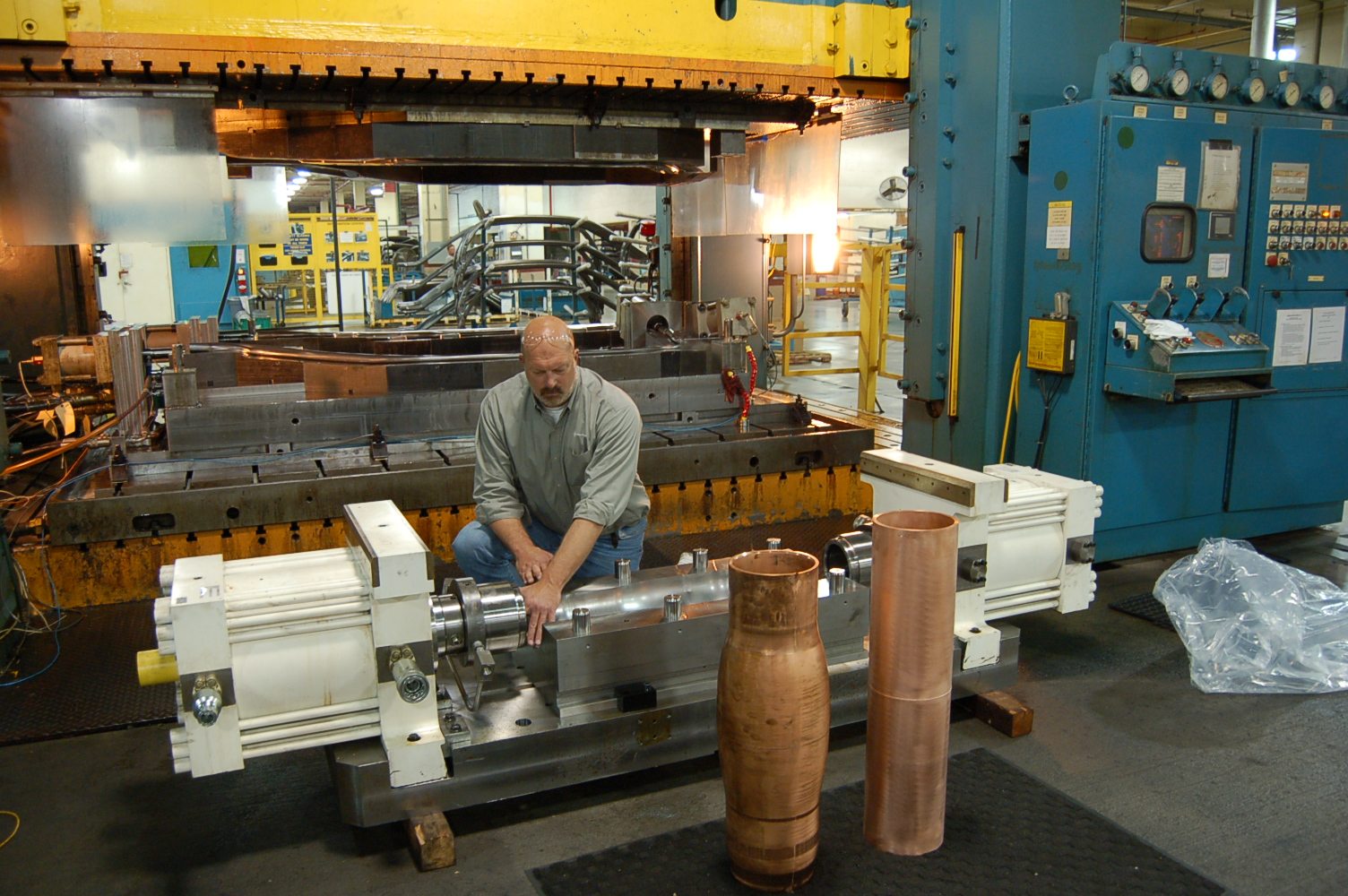
American Hydroformers has slowly built up a niche in the tube hydroforming industry. With nearly 10 years in business, American Hydroformers is ready with expertise, equipment and capacity. Hydroformed components will never replace or completely remove stamped and welded assemblies, however the hydroforming process can delvier a superior component more cost effectively than conventional processes. When looking at the feasibility of having a part or component hydroformed, AHI helps companies look at the technological side of the process to make sure the component will be stronger and lighter, however the business side must be addressed to make sure the component can be made faster or at a lower cost. American Hydroformers can hydroform high-strength, low alloy materials, high yield strength materials up to 650,000 PSI dual phase steels and so on.
To read the full story about American Hydroformers in The Tube and Pipe Journal please contact us.
American Hydroformers was recently spotlighted on the cover of The Tube and Pipe Journal. If you missed the October/November copy let us know and we’ll get you the full story.
Hydroforming is a metal fabricating and forming process which allows the shaping of metals such as steel, stainless steel, copper, aluminum, and brass. This process is a cost-effective and specialized type of die molding that utilizes highly pressurized fluid to form metal. Generally there are two classifications used to describe hydroforming, sheet hydroforming and tube hydroforming. Sheet hydroforming uses one die and a sheet of metal; the blank sheet is driven into the die by high pressure water on one side of the sheet forming the desired shape. Tube hydroforming is the expansion of metal tubes into a shape using two die halves, which contain the raw tube. Hydroforming is used to replace the older process of stamping two part halves and welding them together. It is also used to make parts both more efficiently by eliminating welding as well as creating complex shapes and contours. Parts created in this method have a number of manufacturing benefits including seamless bonding, increased part strength, and the ability to maintain high-quality surfaces for finishing purposes.
Error: Contact form not found.
Leave a Reply