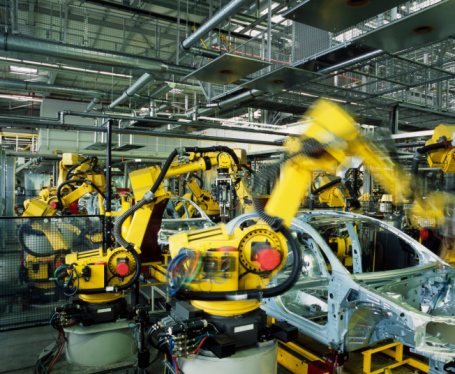
Tube Hydroforming Continues to Pioneer in Auto Manufacturing
Tube hydroforming is continuing to be the lead manufacturer in parts for the automobile and bicycling industry, and it appears as if newly designed models for the 2015 line won't be any different ...

5 Reasons Why Tube Hydroforming is the Future
Though it is a relative newcomer, when compared side-by-side with the conventional process of stamping, tube hydroforming is quickly becoming a formidable technique for the automotive industry's vario ...
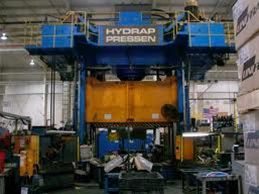
AHI Adds 1800 Ton Hydroforming Press
American Hydroformers Inc. has been supplying parts to the automotive industry for nearly 10 years now. Hydroforming gives our customers the ability to specify lighter weight, stronger parts with the ...