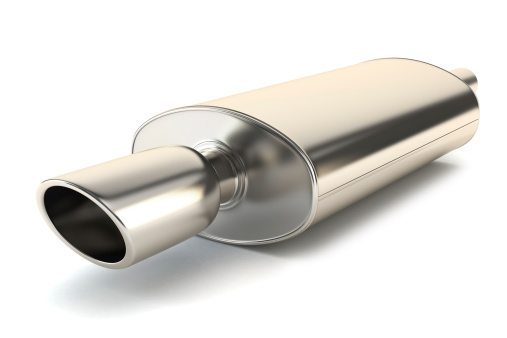
Hydroformed Components Still Huge Part of Manufacturing
We have long highlighted how hydroformed components are integral to manufacturers. From the kitchen sink to sports cars, hydroformed parts continue to lead the charge of innovation, and chan ...
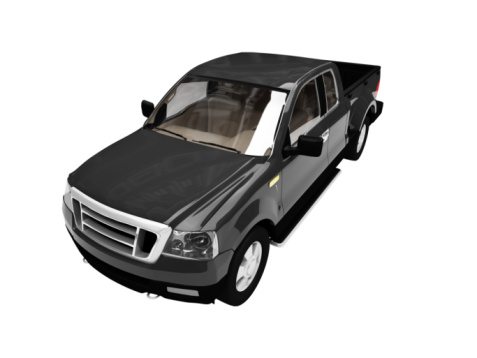
Aluminum Hydroforming Leaves Its Mark
As automotive and mountain-biking companies begin to roll out sneak peeks at their 2015 lineups, it is becoming increasingly apparent just how much new advancements in hydroforming aluminum have affec ...
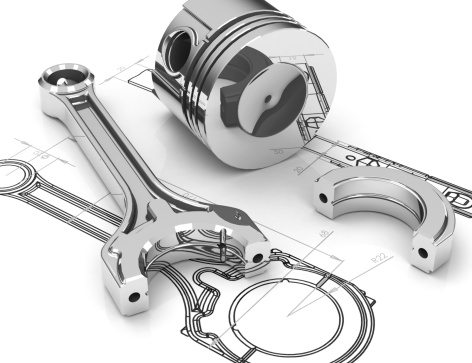
New Vehicles That Have Benefited from Hydroforming
By now, you know that hydroforming is one of the most innovative and ground-breaking methods used to manufacture. Its meteoric rise to greatness has been documented by its progress to redefine how ind ...