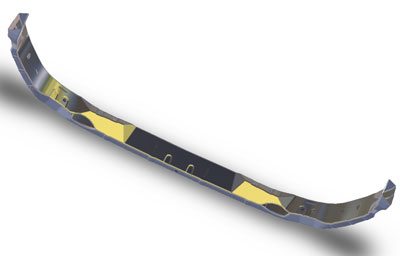
Tube Hydroforming vs. Metal Stamping
Today, nearly all businesses that desire to form parts have concerns regarding the strength, weight, and cost of a component. Metal stamping has been a traditional metal forming procedure. It does not ...

Tubular Hydroforming
Most of us have never considered the world of hydroforming or tubular hydroforming. The components made from these methods have permeated a great many areas of our lives from the vehicles we drive to ...
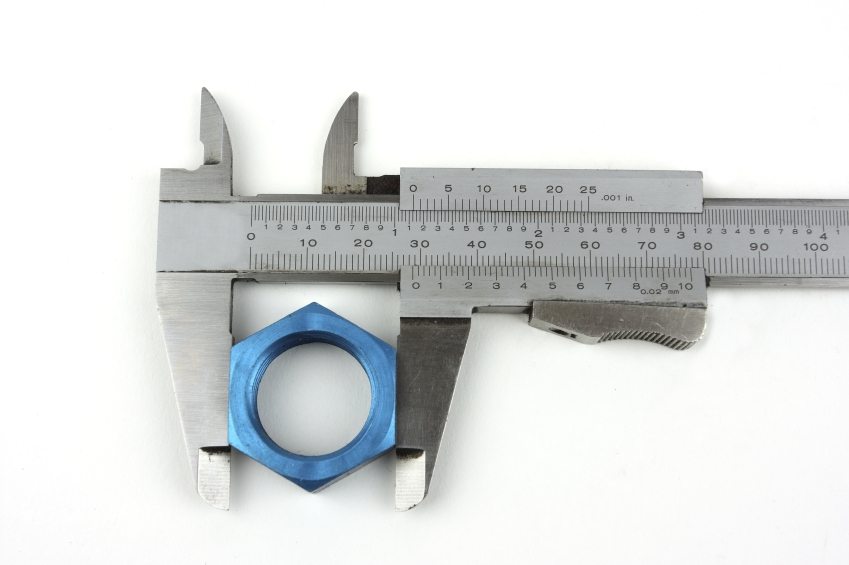
Accuracy in tube hydroforming
As the demands for lightweight construction and precision grow, tube hydroforming is becoming increasingly popular. Hydroforming is used in a wide variety of applications from industry parts to bikes ...

Hydroformed Bicycle Frames
You may think that if you've seen one bike, you've seen them all. Yes, they come in different colors and wheel sizes with different kinds of brakes; but they're basically all the same. After all, they ...

Advantages of Tubular Hydroforming
Any item that is built with a metal tube can be made more efficiently and cost-effectively with tubular hydroforming. The process was first developed and used in the 1950s. The disadvantages of pressi ...