Hydroforming and Its Automotive Application
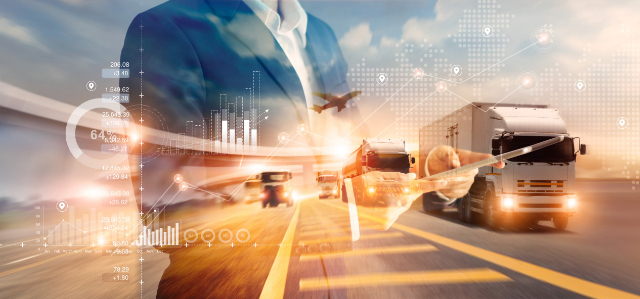
No matter how Fast and Furious one may wish they could be while driving, the notion of a safe car and high probability of accident survival is in the back of many individuals’ minds. Even when buying your teenage kid their first car, thoughts of protection, frame strength, and survivability are all factors that you take into consideration. It doesn’t matter if their 2007 matte gold Honda has a broken A/C system, one of the speakers doesn’t work, and the right passenger window doesn’t roll down – the brakes function, the headlights are bright and the frame is strong enough to protect your kid.
Automotive Application and Innovation
As technology and innovation continue to progress within the automobile industry, questions about the safety of vehicles and cars is always being called into question. These questions often lead to clear preferential and differential lines being drawn between sports cars, sedans, and trucks. While the alloy-make-up of sports cars is terrifying to those worried about car accidents, the prospect of reaching into wealthier markets while also maintaining vehicle durability is not only desirable but attainable. The method in which one can acquire this fusion of automotive characteristics is through Hydroforming technology and processes.
Automotive Application and Hydroforming
As a process, the development of hydroforming technology has gone from shaping aluminum and low alloys to the manipulation of stainless steel. In order to create specific shapes and pieces to build a vehicle (mostly sports cars, at the current moment), hydraulic fluid and pressure is used to press metal alloys down into the desired mold or shape, thus making the development process of automobiles more cost and time-efficient. This method of manufacturing is thus considered desirable not only through its conservation of time and money but also through its ability to create structurally sound and strong metal pieces to be added to lightweight vehicles such as sports cars and sedans. Although the nature of lightweight cars prevents them from having absolute metal frames, the use of hydroforming and application towards the automobile industry lets companies develop vehicles that are just a little stronger and a little faster.
American Hydroformers
Innovation is always growing and finding new ways to break through walls considered to be unbreakable. The emergence of low alloy vehicle-makes has been a high risk, high reward investment for the auto industry (increased risk of mortality, increased possibility for monetary growth). As the popularity of high-tech vehicles grows in public trends, it is important that companies have access to and utilize the technologies that provide the greatest level of benefit for themselves, their products, and their customers. The nature of hydroforming technology in its application towards automobiles and (more specifically) lightweight cars has the capability to provide the structurally sound and safe design of lightweight vehicles while still reaping the benefits of selling to wealthier consumer markets.
For more information, contact us today!
Leave a Reply