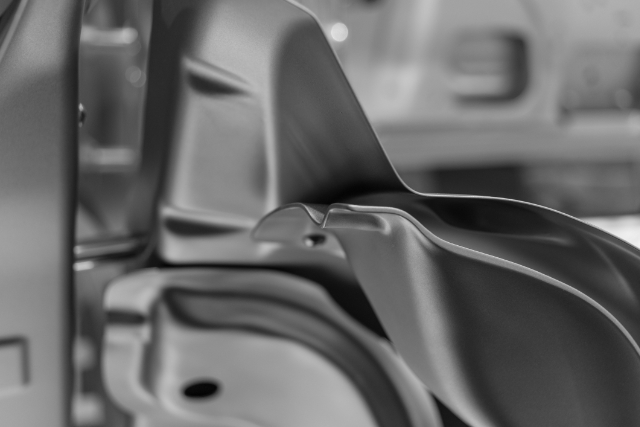
How Is Deep Draw Hydroforming Impacting You?
When you think about hydroforming, you will probably only think about the automotive industry. However, deep draw hydroforming will continue to be a dependable and authentic manufacturing process. Tho …

Changes in Product Requests Do Not Always Escalate Prices
If you wanted a certain part that had intricate geometric shapes
in it and you did not want tool marks or welds, you would want that part to be
created through hydroforming. You do all your research a …

Deep Drawing Continues To Be A Popular Method
When you think about metal forming, what do you generally think about it? It will not be a surprise if one of your first thoughts is deep drawing. Deep drawing is one of the most used and popular meth …
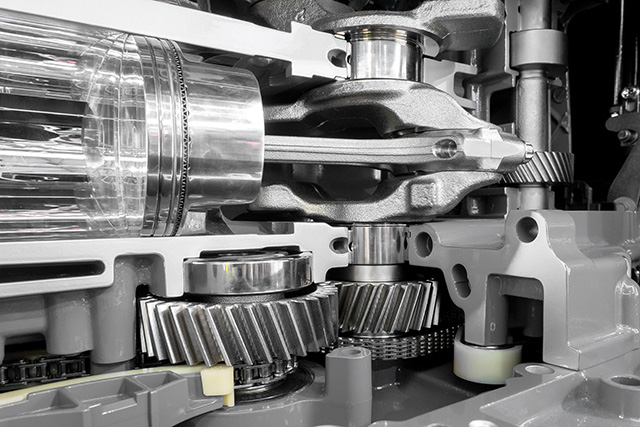
Friction Stir Welding: Its Applications and Advantages for the Automotive Industry
Friction stir welding (FSW) is a relatively new welding process that was invented at The Welding Institute in Cambridge, UK in 1991. FSW is a solid-state joining process that uses frictional heat comb …

Finish Your Project With The Right Hydroforming Process
Hydroforming is the process that involves shaping various metal parts into pieces that are sturdy and light in weight. While this is a very quick and affordable process, it is also very efficient and …
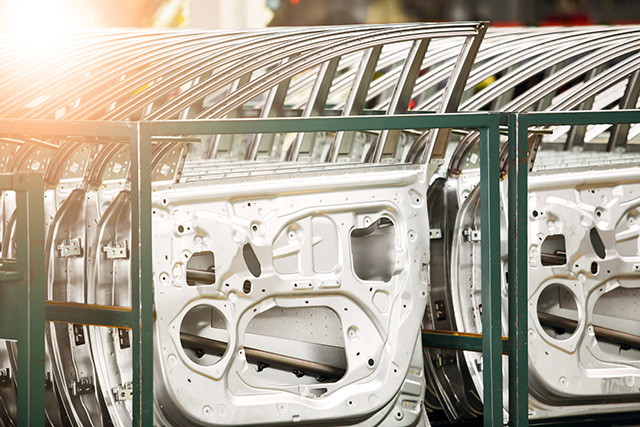
What is Passive Versus Active Hydroforming?
Hydroforming is the process of using pressure on sheets of metal to create shapes, many that are used in building automobiles. For example, if you look at the metal cradle holding the engine in an aut …

Why Is Hydroforming A Preferred Method?
The hydroforming method has been around for more than six decades, but there have been many advancements and innovations that have changed the way each industry thinks about their profits, manufacturi …

FEA Refinements Boost Capabilities
One of the more enjoyable aspects of living in a technological age is the ease with which we can access news and information. At any moment, we can learn about new inventions and fresh developments in …

Hydroforming and the Midwest: Busting Some Myths
Hydroforming and Midwest–both of these terms have seen their share of disinformation. Fortunately, we’re here today on a mythbusting mission, set on clearing the air and setting the record straight.
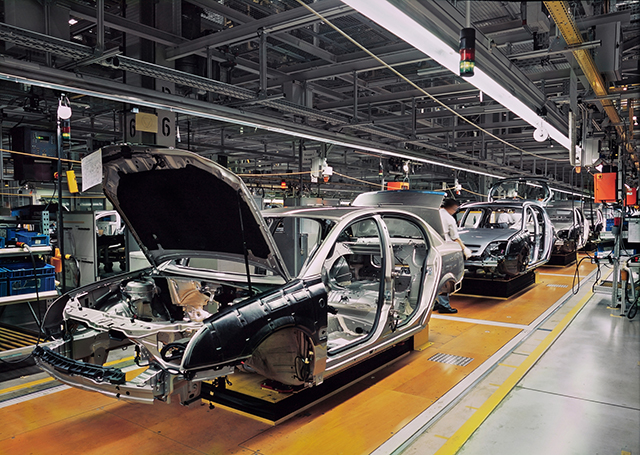
What Is Deep Draw Hydroforming?
For many years, it has been understood that metal stamping or pressing is an effective and economical method for manufacturing parts that are quite complex. Although there may be a higher price to pay …