
What Is Hydroforming: Benefits of Hydroforming
The hydroforming process has been used for quite some time in the manufacturing industry. The hydroforming process involves the use of stainless steel, aluminum, and other ductile metals. These ductil …
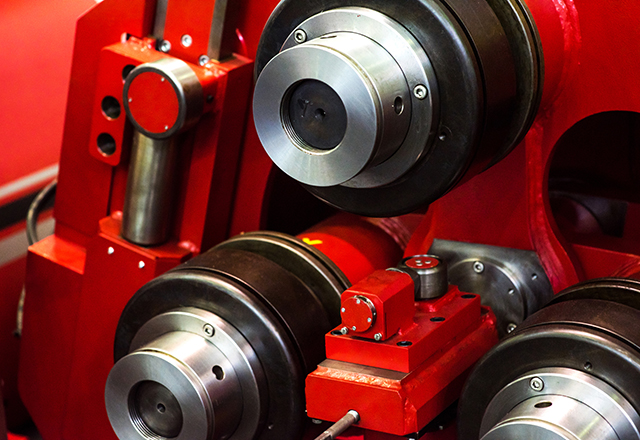
Metal Stamping or Hydroforming: That Is The Question
Since 2003, American Hydroformers has set high standards in the hydroforming industry and has continued to work hard to stay at the top of the manufacturing industry. American Hydroformers continue to …
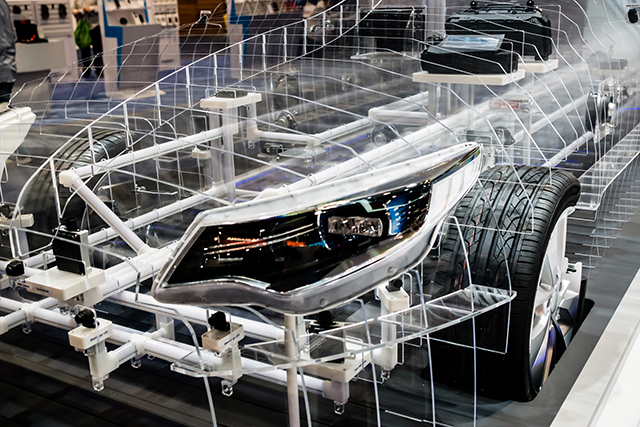
What Should You Know About Deep Draw Hydroforming?
Deep draw hydroforming is constantly in competition with other types of hydroforming processes that are able to create the same products or similar products. However, deep draw hydroforming has multip …
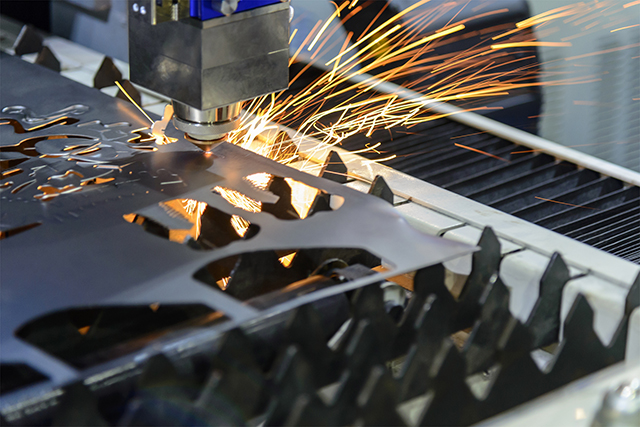
What Is Friction Stir Welding? American Hydroformers
The welding technique, friction stir welding, was developed almost 30 years ago in 1991. Although it was invented many years ago, it has seen a high rise in demand over the past few years. One of the …
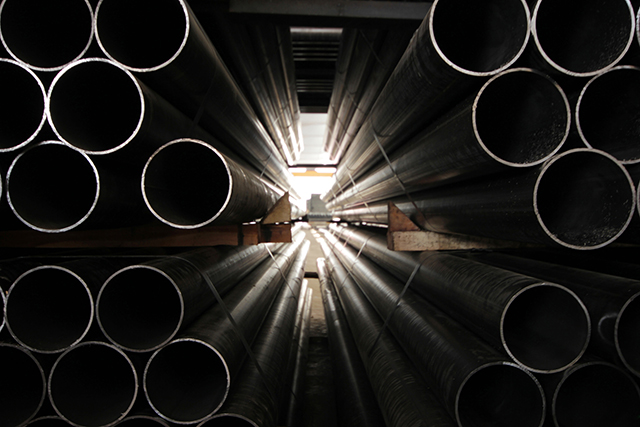
Tube Hydroforming: A Short History
Tube hydroforming: a short history. In many ways, the past holds the keys to the present. If those who have gone before us had not accomplished great things, we would not be where we are today. That’s …

Tube Hydroforming: The Process Behind Lighter Components
One of the main drivers in the automotive industry is the demand for faster processes and lighter components. One of the best methods for delivering lightweight components is known as hydroforming. Hy …
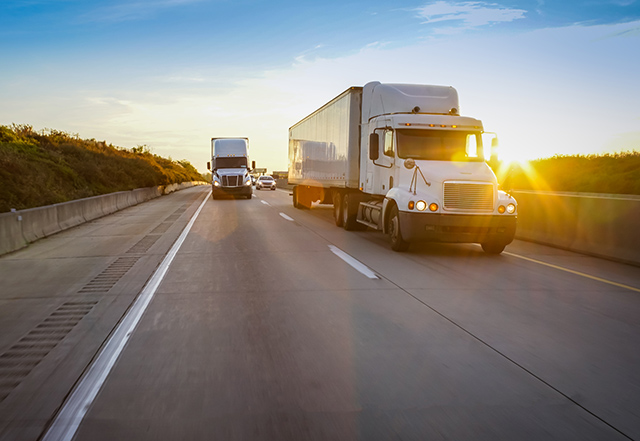
Why Choose American Hydroformers? 3 Good Reasons
When it comes to hydroforming services, you have a few options. Just because you have options, though, does not mean that they are all equally good or good for you. We would like to offer three good r …

American Hydroformers: Getting The Product You Want With Hydroforming
When it comes to hydroforming, many people may think that it is all about making large parts and expensive parts that can be customized and specialized for applications such as automobiles, jet engine …

The Curious Case of the Tesla Model 3
Tesla cars have been around for a while now, and successive models have been called everything from an “all-electric dream car” to an “eco-friendly gift to the motoring masses.” Of course, press for T …
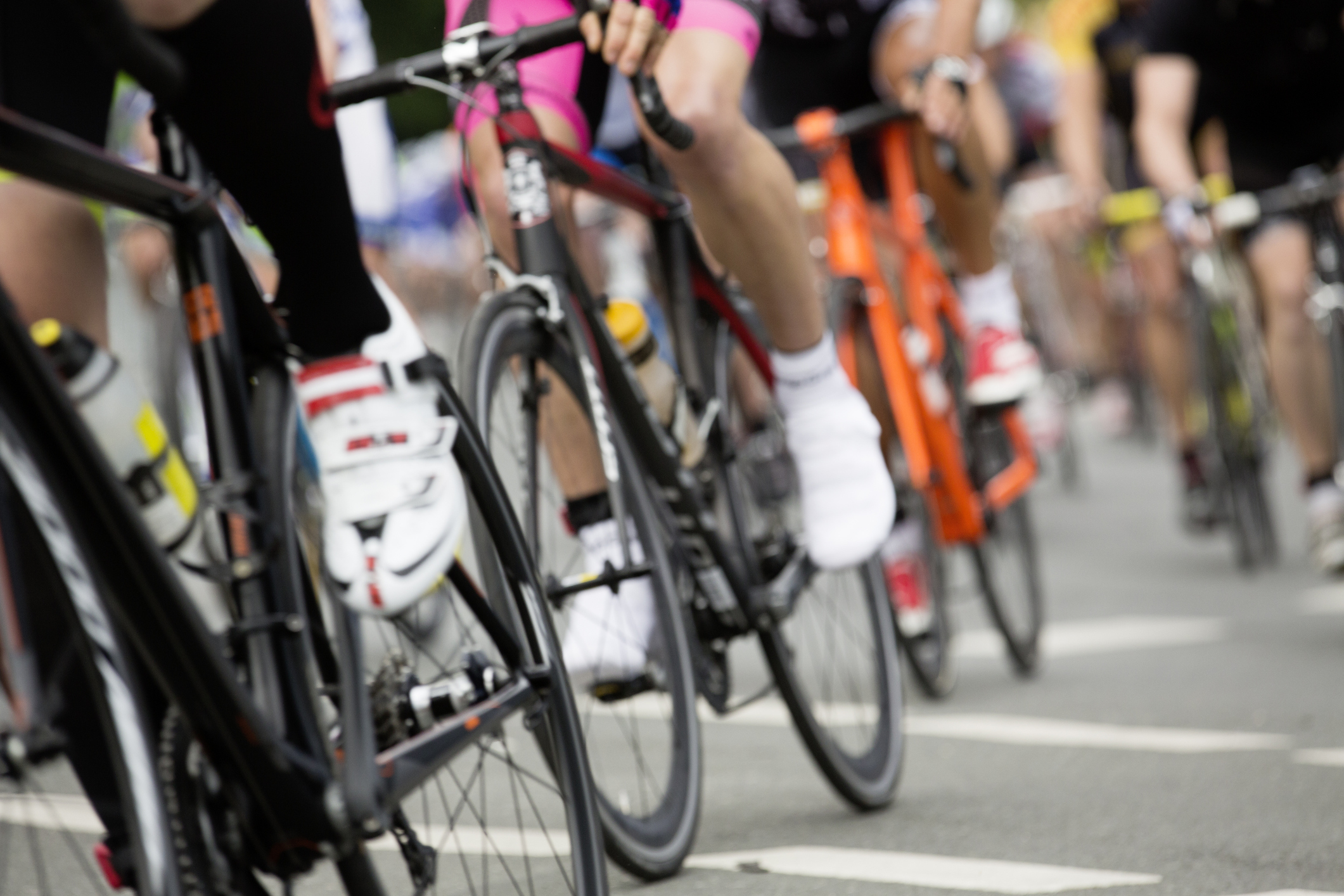
American Hydroformers News Roundup: Spring, 2018
Here at American Hydroformers, we like to keep abreast of the latest developments in the world of hydroforming. Every once in a while, we bring together a few interesting news articles for your instru …