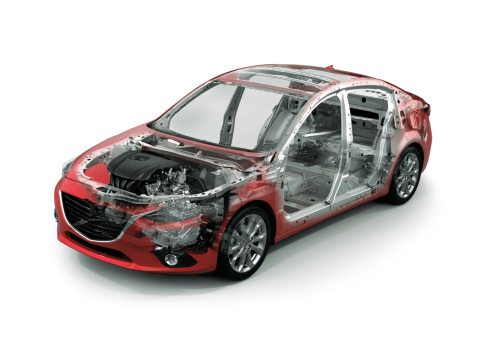
Next Generation Metal Stamping to Grow Significantly Worldwide Over Next Decade
We here at American Hydroformers are big proponents for the metal stamping industry. What began long ago as a means to bolster the manufacturing process into a single stage operation, has co ...
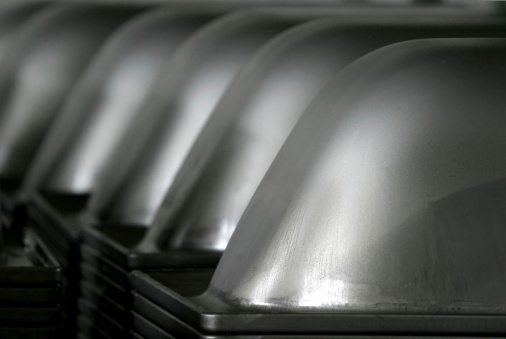
Deep Draw Hydroforming Aids in Medical Device Manufacturing
It has long been established that deep draw hydroforming is a technology that has staying power. The process in which deep draw hydorforming follows makes it a powerful solution for a variet ...
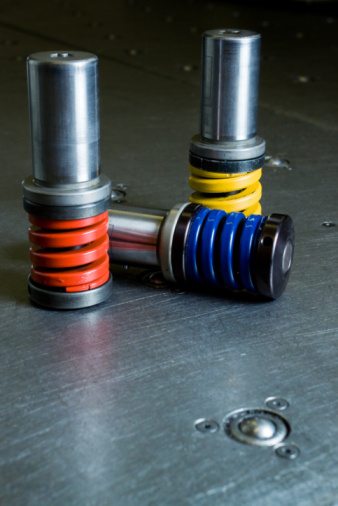
Report Says: Metal Stamping to Increase Thanks to Auto Industry
Metal stamping is a very important process to the manufacturing of automobiles. It plays host and is integral to a broad range of parts and finished goods. It transforms flat sheets of metal into ...
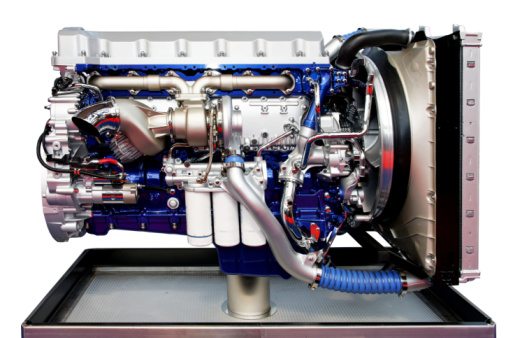
Aluminum Hydroforming Outperforming Steel Stamping
Hydroforming aluminum products has been around for the last few decades in some for or another. In the beginning, it was perfected to manufacture lightweight parts for the automotive industry as cars ...
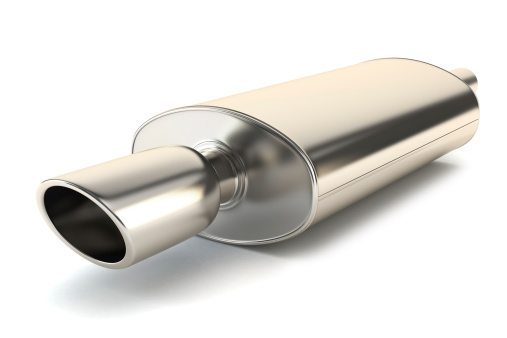
Hydroformed Components Still Huge Part of Manufacturing
We have long highlighted how hydroformed components are integral to manufacturers. From the kitchen sink to sports cars, hydroformed parts continue to lead the charge of innovation, and chan ...