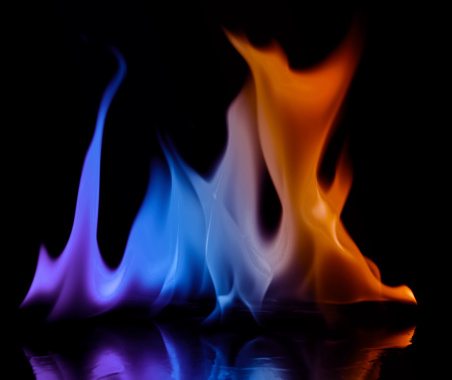
High-temperature Metal Gas Forming
With the use of hydroformed parts becoming increasingly common in the automotive and cycling worlds, many people are now more aware of the process used to shape ductile metals into pieces that are bot ...

American Hydroformers Explains How Internal High Pressure Hydroforming Works
American Hydroformers is on the cutting edge of production technology. We offer many services, including metal fabrication solutions through the use of hydroforming, laser cutting, and several ot ...
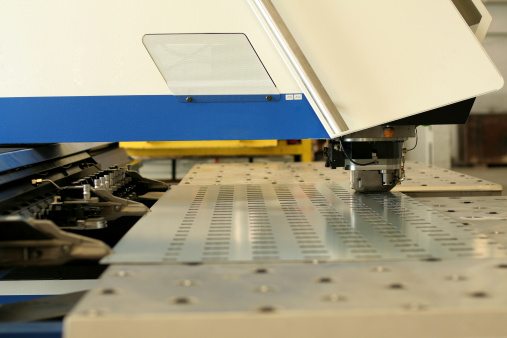
Hydroforming Versus Stamping
Hydroforming versus Stamping? That is the question. Metal stamping has been used in the production of consumer goods and products for a very long time. Some even believe that the history of metal st ...
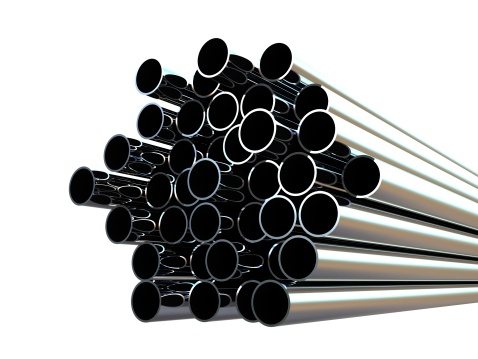
Hydroforming DP 780 Steel Tubes
The advancement in high strength steel can be seen by the use of hydroforming DP 780 Steel tubes . It provides an innovative technology that can not only lower the cost of steel frame fabrication, but ...

Innovative Uses of Sheet Hydroforming
Most consumers are already fairly well aware that one of the most common applications of sheet hydroforming is found in the automotive sector. For years, auto makers have taken advantage of hydroformi ...
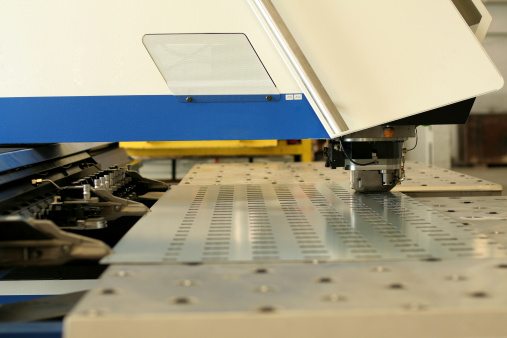
Advancements in Metal Stamping
Hard on the heels of the announcement that General Motors has opened a new metal stamping plant in Arlington, Texas, comes further information regarding how the opening of this new plant has impacted ...
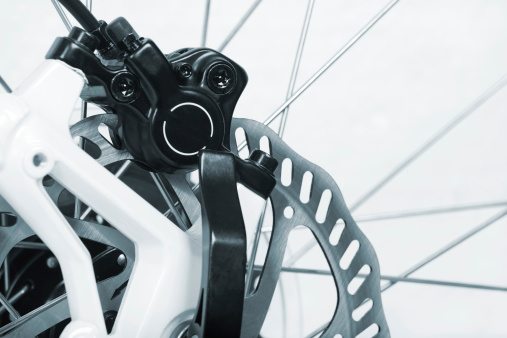
Hydroformed Components: New Metals on the Market
There has been recent news about hydroforming bringing titanium to the masses. Until recently, it was difficult to use titanium on a commercial scale because of the cost as compared to the more afford ...

Understanding Metal Stamping and Its Many Uses
Metal stamping is a process which includes the stamping or pressing of sheet metal into different forms. Some of the different types of metal stamping include punching, deep drawing, pressing, embossi ...

Hydroforming Advantages for Automotive
Hydroforming metal is one of the most cost effective ways of creating asymmetrical parts for the automotive industry. Many parts used on cars today have irregular shapes making traditional methods of ...

Advantages of Tubular Hydroforming
Any item that is built with a metal tube can be made more efficiently and cost-effectively with tubular hydroforming. The process was first developed and used in the 1950s. The disadvantages of pressi ...