What is Tube Hydroforming? The History and Background Explained
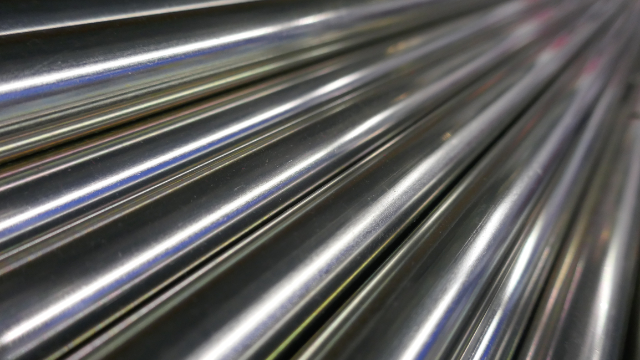
First developed in the late 1940s and early 1950s, tube hydroforming is the process by which pressurized fluid, either hydraulic fluid or water, is used to expand and shape metal tubes into the contours of a die. Since there are no welded seams, tubular hydroforming can be used to fabricate structural parts that are lighter, more rigid, and stronger than stamped sheet metal.
In the tubular hydroforming process, a tube is placed into a forming die. The ends of the tube are sealed, and the tube is filled and pressurized with fluid. The internal pressure forces the tube to form the shape of the tool cavity. This allows for complex shapes to be manufactured in a single step, giving tighter tolerances and a smoother finish over more traditional stamping methods, and can also lessen the effects of spring back in the finished product. Hydroforming makes it possible to create tubes for any unique fit and provides improved consistency by reducing dimensional variations.
What Is Tube Hydroforming?
New materials are constantly being researched, but almost any ductile metal, such as aluminum, steel, stainless steel, copper, or brass can be shaped at room temperature from tubular blanks.
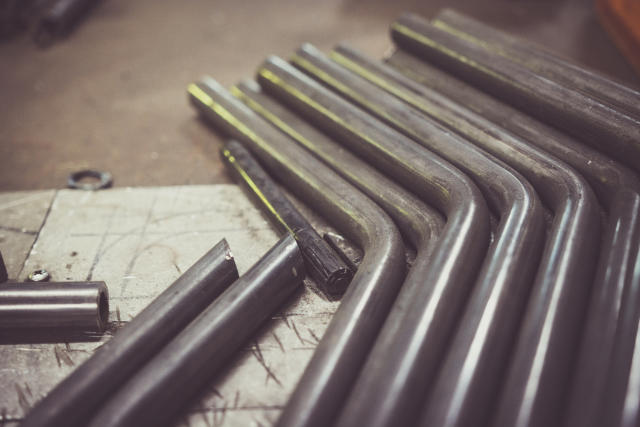
Heavily used in the automotive, bicycling and other industries, there is a growing demand for hydroformed products. Using this method, experts can fabricate products to suit almost any structural application, typically at lower costs than more labor-intensive processes that require extra handling for additional steps such as welding or drilling. Parts can also be formed without the scratches and tool marks normally associated with stamping, so less labor is involved in smoothing and polishing.
American Hydroformers
American Hydroformers specializes in tube hydroforming. We also offer laser cutting, etching, and trimming of your finished products. Contact us today to learn how we can improve your design performance and enhance your company’s cost-effectiveness for this and many other fabrication needs.
You can also follow us on Twitter.
Leave a Reply