Mercedes-AMG selects hydroformed parts
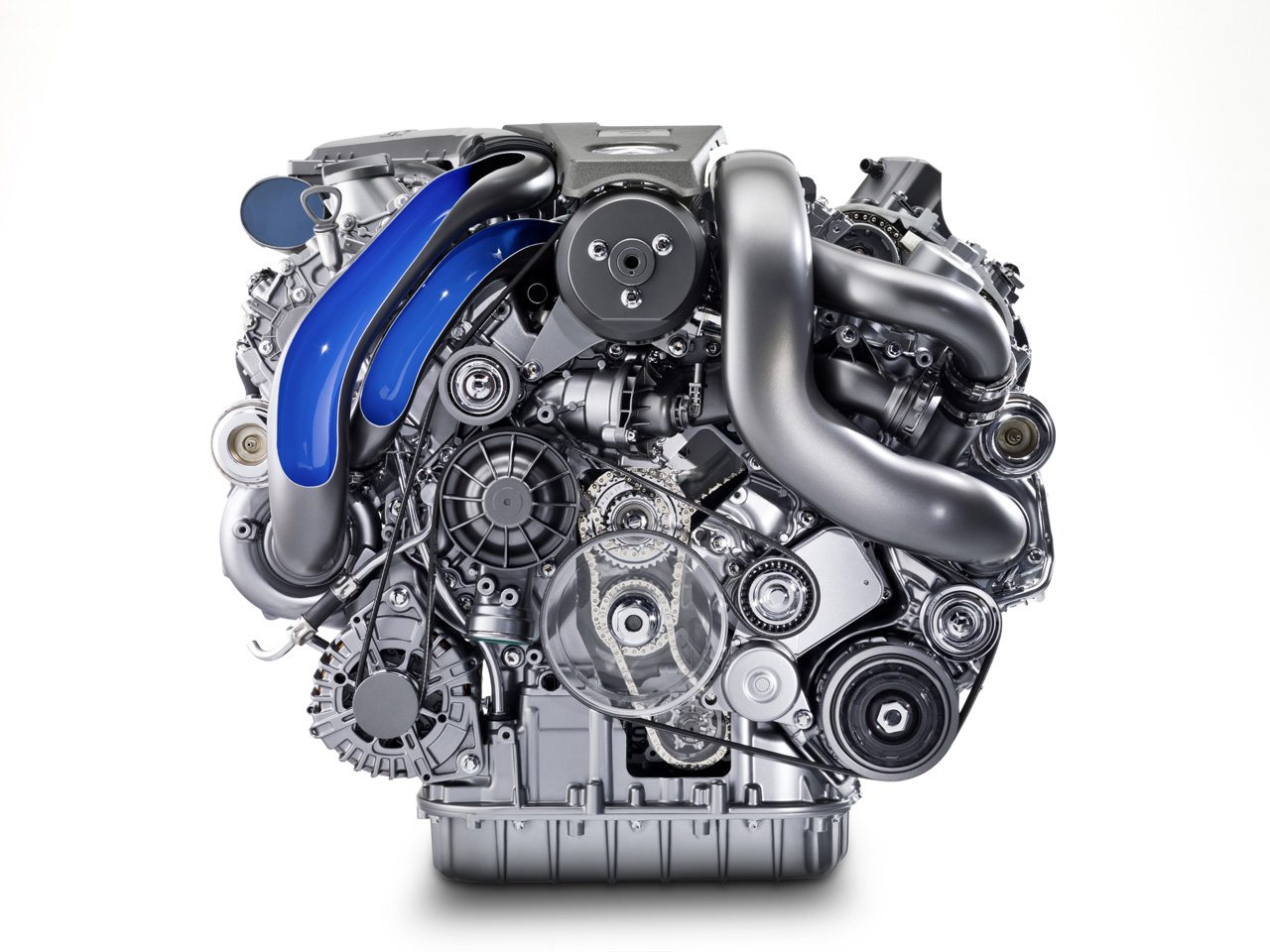
As more and more automotive engineers begin to learn and source more hydroformed parts and components, the hydroforming industry sits on the verge of rapid growth. Mercedes-AMG selects hydroformed parts for its new CL63 intake. Mercedes -AMG engineers found the hydroformed intakes to be “extremely short charge-air ducting makes for outstanding responsiveness. The stainless steel pressure pipes for the fresh and charge air are produced by the hydroforming process, have a wall thickness of only 0.03 inches and are designed for very low pressure loss.” Again, the benefits of using hydroformed parts to remove costly processes like welding not only remove labor and quality constraints, but it gives the manufacturer the ability to use the proper gauge material while removing unnecessary weight at the same time.
High performance and race cars have long used tubular frame construction for its strength and light weight nature. With the latest federal mandates for mileage and crash worthiness, hydroformed frames are a good solution.
Error: Contact form not found.
Leave a Reply