
Deep Drawing Continues To Be A Popular Method
When you think about metal forming, what do you generally think about it? It will not be a surprise if one of your first thoughts is deep drawing. Deep drawing is one of the most used and popular meth …

Hydroforming and the Midwest: Busting Some Myths
Hydroforming and Midwest–both of these terms have seen their share of disinformation. Fortunately, we’re here today on a mythbusting mission, set on clearing the air and setting the record straight.
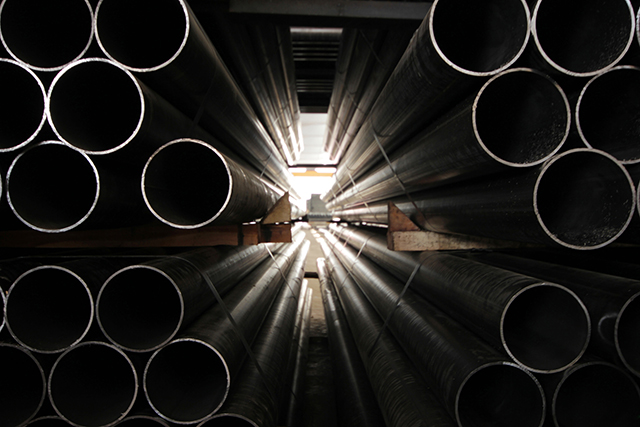
Tube Hydroforming: A Short History
Tube hydroforming: a short history. In many ways, the past holds the keys to the present. If those who have gone before us had not accomplished great things, we would not be where we are today. That’s …

American Hydroformers: Getting The Product You Want With Hydroforming
When it comes to hydroforming, many people may think that it is all about making large parts and expensive parts that can be customized and specialized for applications such as automobiles, jet engine …

Is the Pressure to Meet CAFE Standards Rising or Falling?
Are CAFE standards rising or falling? If we know one thing about American policy and lawmaking, it’s that nothing stays static forever. Over the past centuries of our country’s history, we’ve enacted …
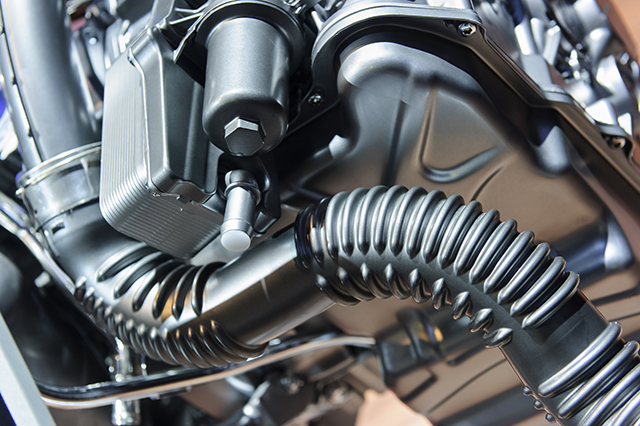
American Hydroformers: Hydroforming in the Automotive Industry
Hydroforming is a fabrication method that is regularly used in the transportation and automotive industries. Hydroforming is used so often because it allows even the most complex shapes to be created …

Casting Vs. Metal Stamping: Should Metal Stamping Be Your Choice?
Casting vs. metal stamping: should metal stamping be your choice? Working with metal is not a new method of manufacturing. Since the middle of the 1800s, a large number of metal forming operations sta …

Tubular Hydroforming for Motorcycle Frame Manufacturing
Motorcycle frame manufacturing is an ideal match for hydroforming technology. Motorcycle performance is a function of power and weight. Anything that can help reduce weight on a motorcycle without com …

Want to Build Your Own Droid? Advances in Aluminum Hydroforming Make It Possible
Want to build your own droid? Advances in aluminum hydroforming make it possible.
No one would deny the sheer popularity of the Star Wars franchise. Talking about the cultural impact of the Star Wars …
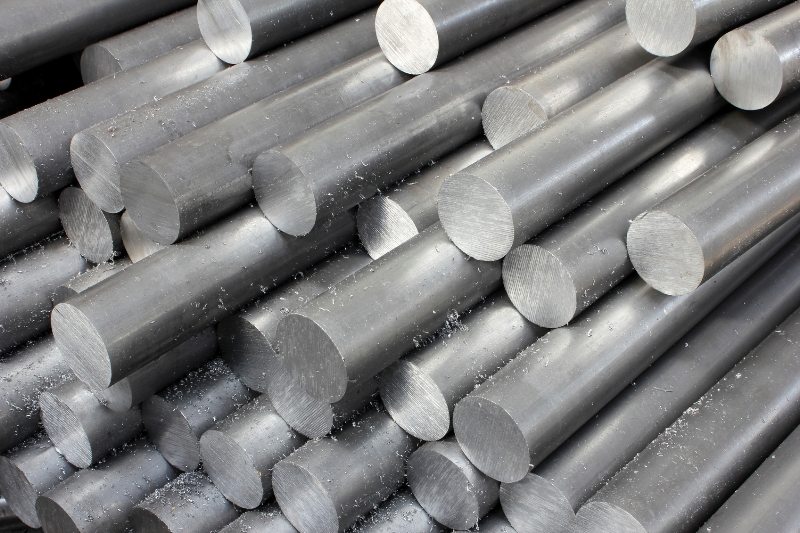
Higher Value Increases Use of Aluminum in Vehicles
In 2015, Ford’s F-150 was the first high-volume vehicle produced with an aluminum frame, reducing the F-150’s weight by 700 pounds. Since then, the need for strong, lightweight material is driving a s …