Pressure and Tube Hydroforming: American Hydroformers
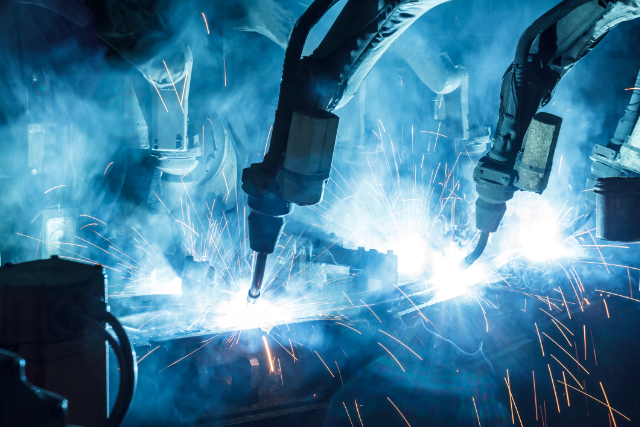
Tube hydroforming is accomplished in one of two ways, either high pressure or low pressure. The desired shape and strength of the metal tube determine the level of pressure that will be used.
High Pressure Tube Hydroforming
High-pressure tube hydroforming is often referred to as internal high-pressure forming. A tube of metal is inserted into the die. High pressure is used to form a tube of desired shape and size. What is a key understanding of high-pressure tube hydroforming is that the shape is obtained with pressure from the inside of the tube. The amount of pressure determines the size and shape of the tube and even the strength of the tube.
Low Pressure Tube Hydroforming
Low-pressure tube hydroforming is similar to high pressure. The difference is the amount of pressure used and therefore the amount of stretching that can be accomplished. In low-pressure tube hydroforming, the pressure is applied before closing the die and that means the circumference of the tube remains relatively the same.

Both high-pressure and low-pressure tube hydroforming are important processes in the manufacture of automobile and airplane parts. If you look under a car or truck you will see various tubes that were formed through tube hydroforming. We want those tubes to have uniform shape and be strong, so they withstand weather and are able to last for a long time. If you look at the interior parts of an airplane you will notice many parts that were created through tube hydroforming. Tube hydroforming adds to the strength of these parts so the vibrations of flying through the air do not damage the parts.
Tube hydroforming is not a complicated process, but it is a valuable process that impacts all of our lives every day. If you would like to learn more, pleaseĀ contact us and we would love to talk to you.
Leave a Reply