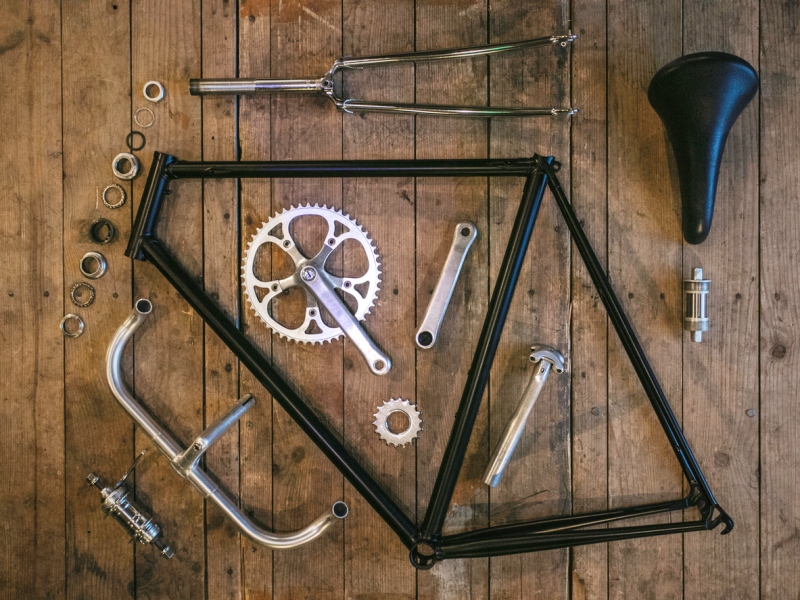
Hydroformed Components Keeping American Commutes Healthy and Affordable
Hydroformed Components Keeping American Commutes Healthy and Affordable. Recently there has been a sudden uptick in the number of people who bike to work instead of driving cars or taking public trans …

Friction Stir Welding: Applications That Are Far Out and Close to Home
Friction Stir Welding: Applications That Are Far Out and Close to Home. Liquid hydrogen, it’s a substance that has fascinated mankind since the 1800s. That’s when James Dewar unleashed it as well as h …
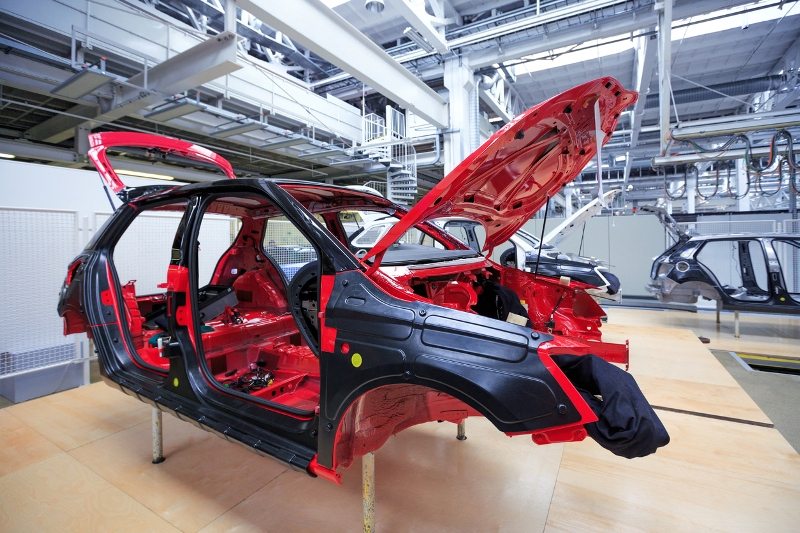
Hydroforming: Moving Us into the Future
Every once in a while, a modern storyteller will encourage readers to consider how the would change if something in the past had shifted in a different direction. This genre is called Alternate Histor …

Current CAFE Standards Help Save Money All Around
CAFE Standards Help Save Money All Around. Much has been written in recent days about the state of the U.S. economy. While we are certainly not a poor nation, if we compare ourselves now to ourselves …
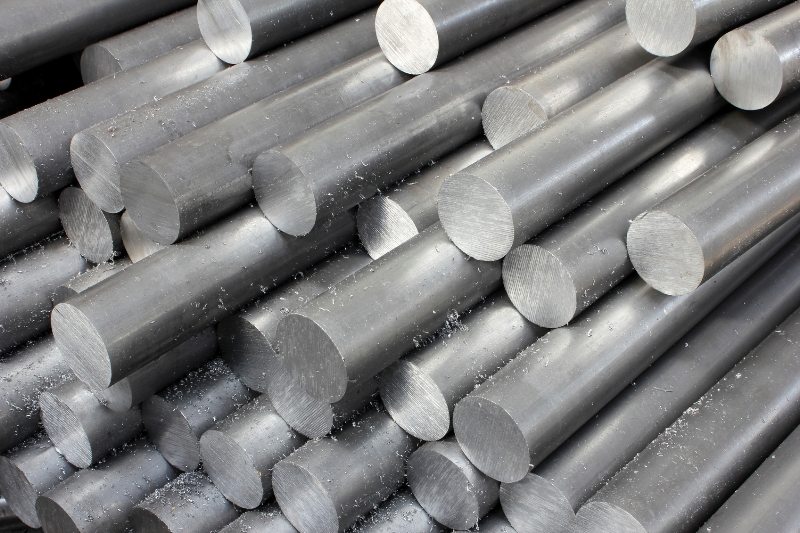
Higher Value Increases Use of Aluminum in Vehicles
In 2015, Ford’s F-150 was the first high-volume vehicle produced with an aluminum frame, reducing the F-150’s weight by 700 pounds. Since then, the need for strong, lightweight material is driving a s …

A World Without Hydroforming
Since the 1990s, hydroforming has been revolutionizing specific aspects of various industries. Advances in hydroforming have affected our lives more than most of us even know. The best way to prove th …

Tube Hydroforming Updates: News Snippets from Around the Web
Beginning in the 1970’s, the process of tube hydroforming has met the increasing demand for the manufacture of simple, lightweight components. Over the next few decades, this process has developed to …

Lightening the Load to Meet Consumer and CAFE Standards
In a world where more and more emphasis is being placed on leaving fewer carbon footprints, fuel economy has become an important issue for auto manufacturers across the country. Not only are auto manu …
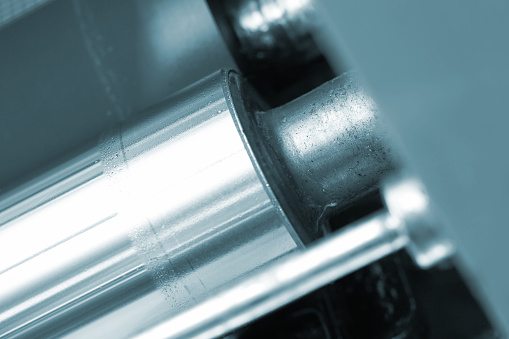
Metal Stamping and Hydroforming: High-Quality Work at a Low Cost
When you are working with metal, you will find that there are a variety of options and tools available for you to use. Although there are so many options for you to choose from, many companies decide …
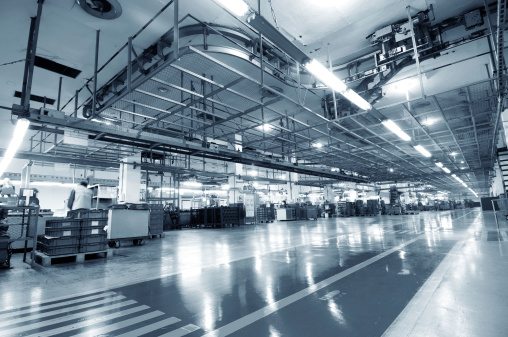
What Is Hydroforming: The Basics
Hydroforming is a unique process used to form metal. As a unique process, it also solves unique problems. Hydroforming makes a number of products possible that wouldn’t be possible through mainstream …