
Sheet Hydroforming: 4 Advantages
Sheet hydroforming is a process that uses liquid as the medium of energy transfer to form the workpiece. Hydroforming is applied more and more in industry because it results in a better strain state i ...

Benefits of Tubular Hydroforming
Since the 1950s, tubular hydroforming has become a staple in the metal fabrication industry. Technological advancements in computer controlling and high-pressure hydraulic systems have allowed the pro ...

Tube Hydroforming White Paper
Tube hydroforming is at the heart of the process that enables modern-day life to proceed more efficiently. From the water piping systems of local utilities to the cars we drive and bikes we ...

Hydroforming Advantages for Automotive
Hydroforming metal is one of the most cost effective ways of creating asymmetrical parts for the automotive industry. Many parts used on cars today have irregular shapes making traditional methods of ...

Hydroforming for Performance in the Automotive Industry
Automakers face a number of challenges in providing consumers with vehicles that are safe, fuel efficient and reliable. One way they are achieving these goals is with the use of hydroformed automotive ...

What Is Tube Hydroforming? All you need to know.
Whether you are well-informed or brand-new to the subject, here is a primer on the basics of tube hydroforming. Read on to discover more about the process, the materials, the products, and the benefit ...
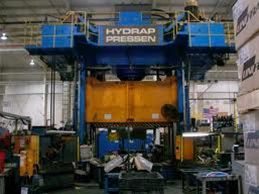
AHI Adds 1800 Ton Hydroforming Press
American Hydroformers Inc. has been supplying parts to the automotive industry for nearly 10 years now. Hydroforming gives our customers the ability to specify lighter weight, stronger parts with the ...