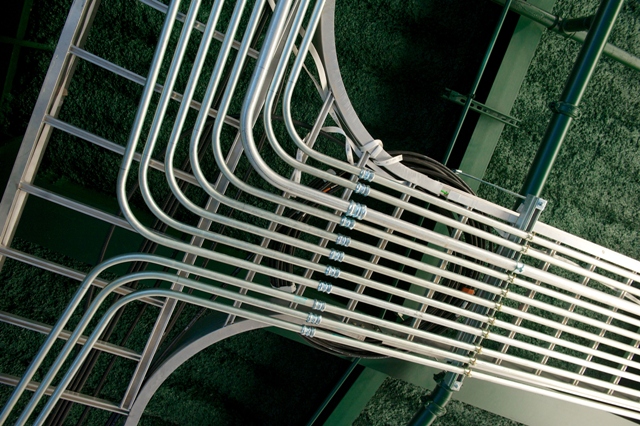
Where Would We Be Without High-Temperature Metal Gas Forming?
Although your average American probably has not heard of high metal gas forming, that does not mean they have not taken advantage of products made possible (or made better) through it. Those of us in …
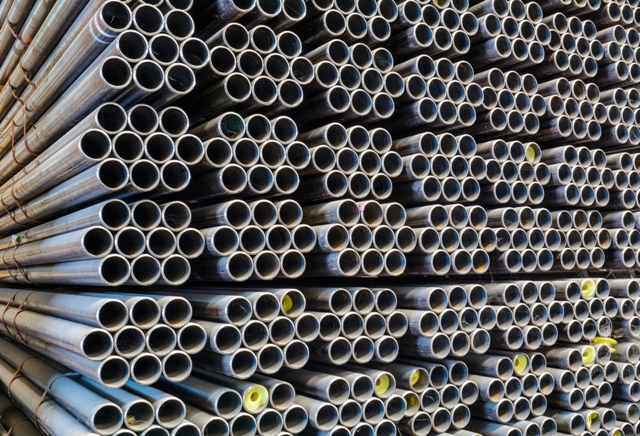
Up Your Tube Hydroforming Game
If your product requires hydroformed components – particularly tube hydroforming – then you have come to the right place. Here at American Hydroformers, we consider ourselves experts in delivering con …

Three Reasons to Consider American Hydroformers
Whether you’ll soon be needing hydroforming services, are looking to leverage the benefits of pre-production Finite Element Analysis (FEA) for your product prototype, or are just shopping around becau …

What is Tube Hydroforming: an Explanation of an Important Procedure
Overview of Tube Hydroforming
Tube hydroforming is one of two groups within the broader category of hydroforming itself, along with sheet hydroforming. It is a relatively new manufacturing process, …
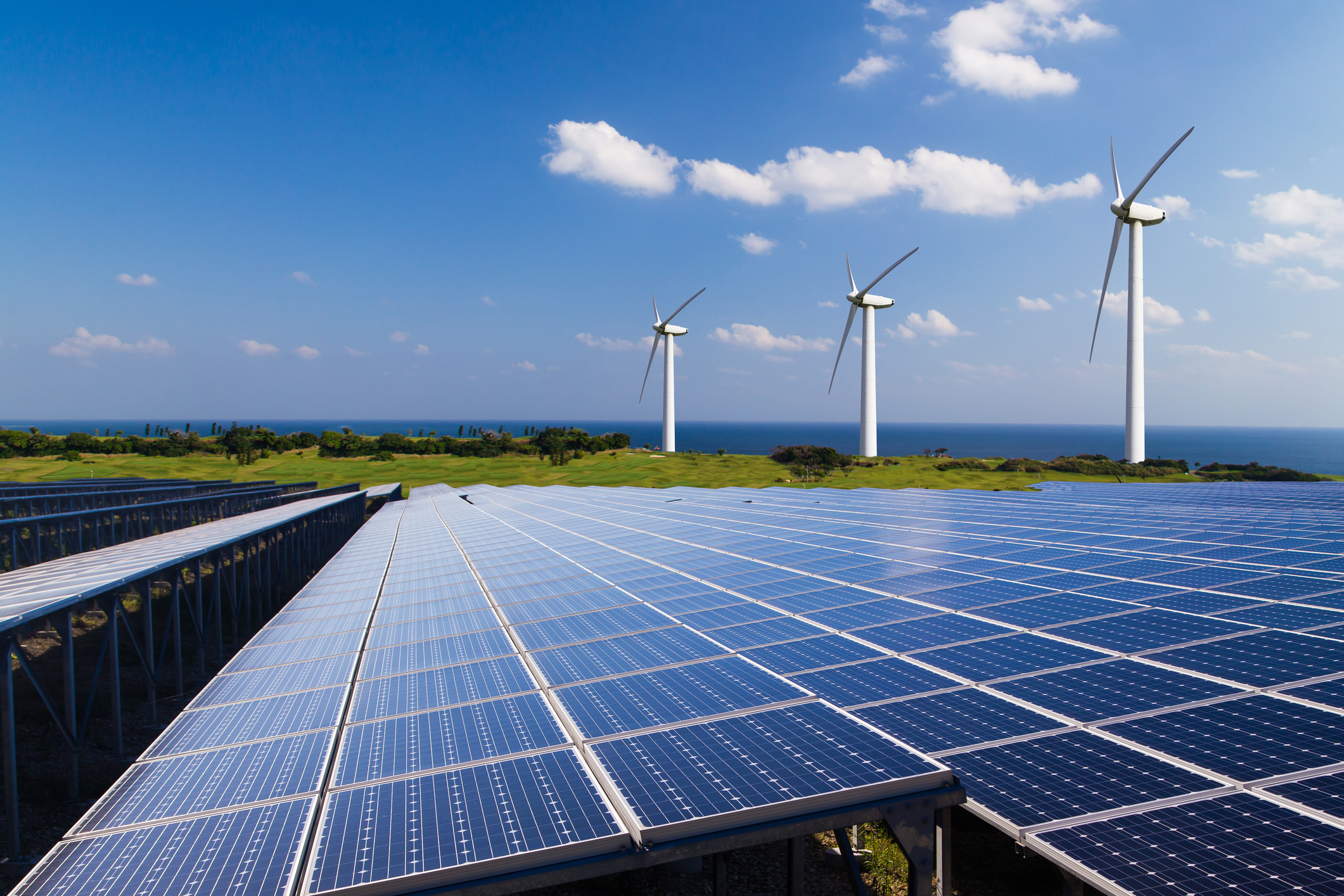
American Hydroformers: The advantages of deep draw hydroforming
If you need a lightweight metal part with a depth larger than the radius, deep draw hydroforming is the way to go. This versatile process makes lightweight, durable parts that are deeper and more accu …
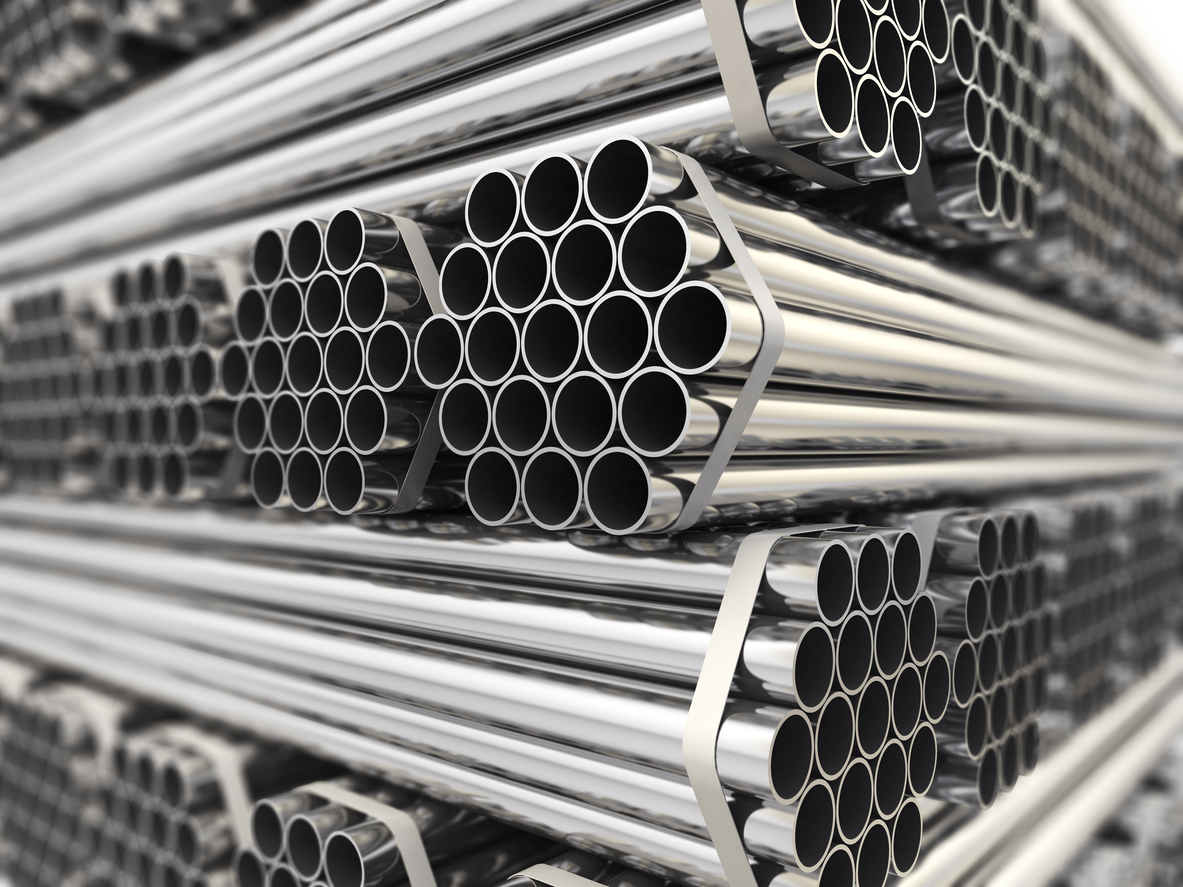
Three Reasons to Choose American Hydroformers
Not every company needs to avail itself of hydroforming services. We know that. As leaders in the industry, we are also aware of increasing demand for our services. In fact, as businesses grow, they …

Cafe Standards in Daily Life: American Hydroformers
Those who work outside very specific industries, such as the hydroforming or automotive industries, probably do not give much thought to current CAFE standards. In fact, many of them might not even be …
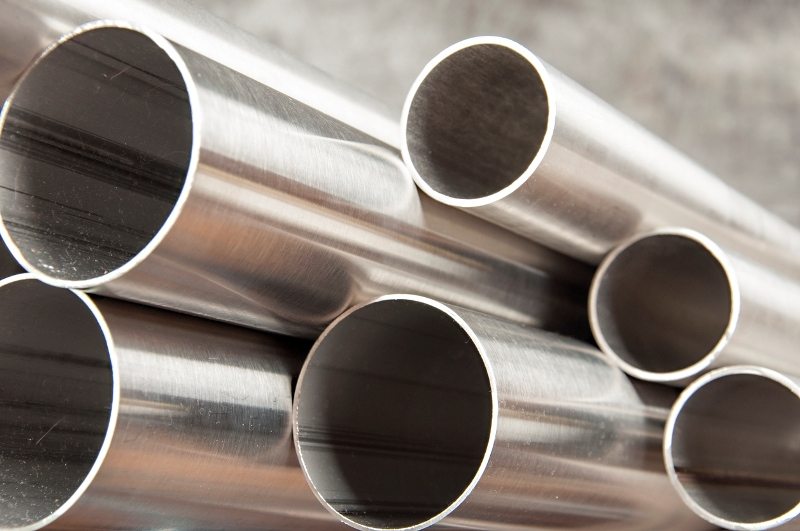
American Hydroformers Can Take You from Prototype through Production
Whether you’re looking to build a prototype fresh from the drawing board or to manufacture your already proven components on a small or large-scale, American Hydroformers can handle your fabricating n …
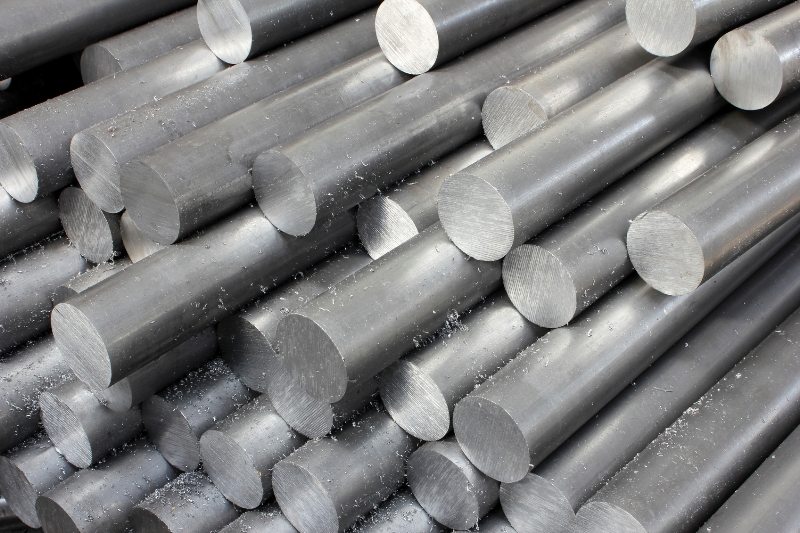
Higher Value Increases Use of Aluminum in Vehicles
In 2015, Ford’s F-150 was the first high-volume vehicle produced with an aluminum frame, reducing the F-150’s weight by 700 pounds. Since then, the need for strong, lightweight material is driving a s …
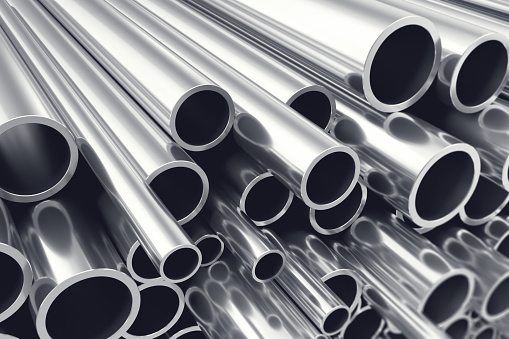
Advantages of Hydroforming in the Mid-West
The advantages of hydroforming are many. Mostly, they revolve around material efficiency, speed and cost savings. Traditional deep drawing methods suffer from the effects of drawing stress (on the mat ...