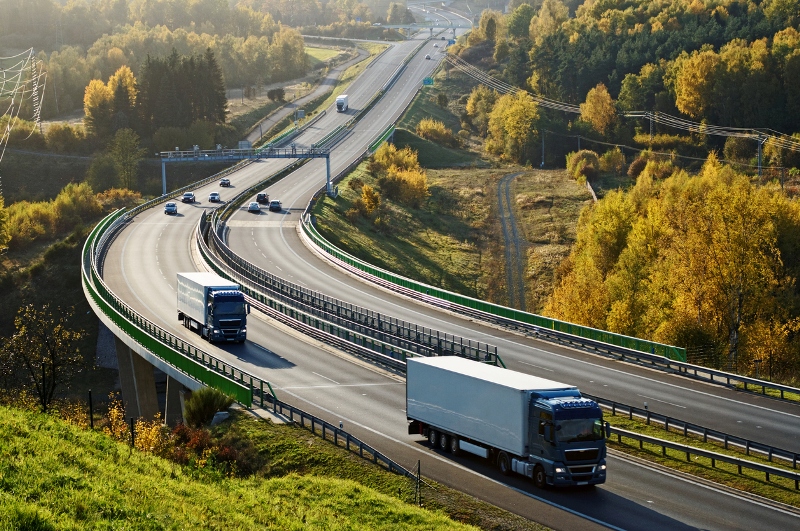
Hydroforming for Beginners: What It Is and Why It Matters
Here on the blog, we enjoy bringing you regular posts about the benefits of hydroforming. Today we’d like to take a step back and present a lesson on hydroforming for beginners: what the process entai …
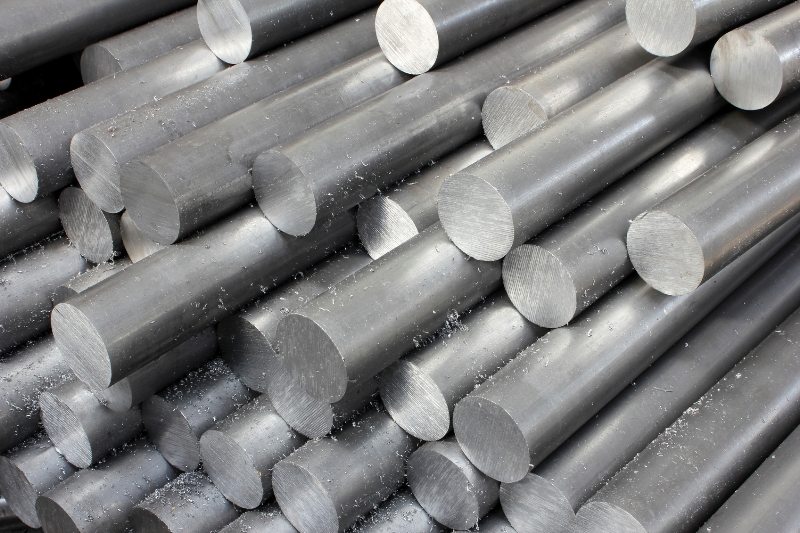
Higher Value Increases Use of Aluminum in Vehicles
In 2015, Ford’s F-150 was the first high-volume vehicle produced with an aluminum frame, reducing the F-150’s weight by 700 pounds. Since then, the need for strong, lightweight material is driving a s …

What is Tube Hydroforming?
Tube Hydroforming is a type of die forming that is used to shape certain metals, including aluminum and stainless steel, into strong but lightweight pieces. This method is often used in the automotive …

Finite Element Analysis strengthens hydroformed parts and customer relationships
When your product represents a structural component of your customer’s purchase it sure better be structurally sound. Who can afford a costly recall or, even worse, be responsible for a personal accid …
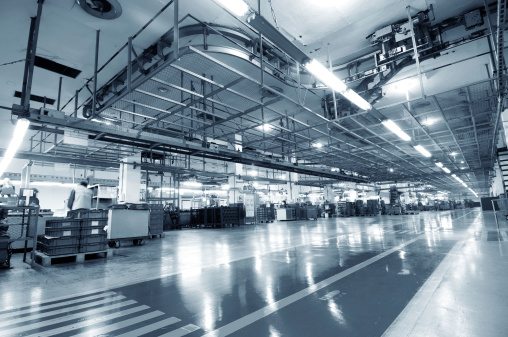
What Is Hydroforming: The Basics
Hydroforming is a unique process used to form metal. As a unique process, it also solves unique problems. Hydroforming makes a number of products possible that wouldn’t be possible through mainstream …

FEA or Finite Element Analysis Implementation: Are You Ready To Make The Step?
It does not matter where you look, you will always find information on how various companies and organizations have used an engineering simulation as part of their strategy when it comes to developmen …

Tube Hydroforming vs. Sheet Hydroforming: What is Hydroforming?
What is hydroforming? Hydroforming is when the force of water, hydraulic fluids, or oils is used to shape a single part. There are two types of hydroforming and each has uses when creating products fr …
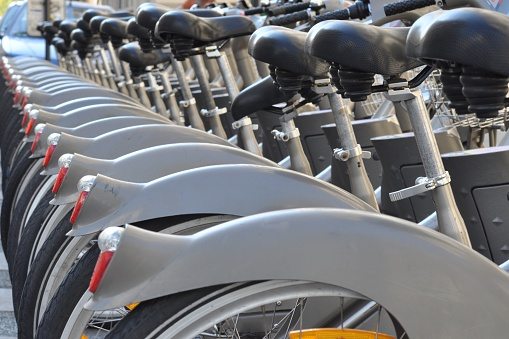
Deep Draw Hydroforming Benefits Your Daily Life
As deep draw hydroforming continues to become a reliable and viable source of production, people who rely on hydroformed parts can only benefit from its persistent innovation.
Information about new a …

What is Hydroforming?
What is hydroforming? Hydroforming is an innovative method of pressing metal into the desired shape. It produces results similar to cold forming, but instead of simply pressing the metal with a mold ...

Improving the World with Hydroforming
Hydroforming is a cost-effective way of shaping ductile metals into stiff, strong and lightweight pieces. Practically all metals that can be cold formed are suitable for hydroforming, and without bei ...