
Tube Hydroforming and Its Impact on the Automotive Sector
It is certainly easy to see how tube hydroforming has transformed certain aspects of the automotive industry. At least, it is easy to see if you know what tube hydroforming is.
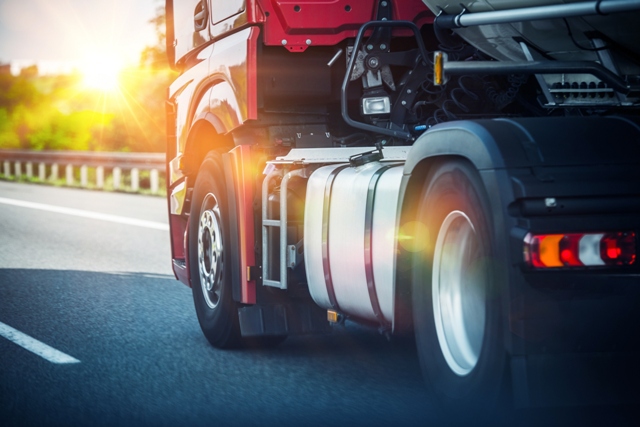
The Automotive Industry and High-Temperature Metal Gas Forming
Although the process of high-temperature metal gas forming may not be common knowledge, most people benefit from this process on a daily basis. They just don’t know that they do.

Tube Hydroforming: Quality Matters at American Hydroformers
Sometimes when we’re in a hurry, we’re willing to sacrifice quality for speed. For example, if we’re hungry but don’t have time to stop at a sit-down restaurant, let alone buy ingredients and cook our …

Three Reasons to Consider American Hydroformers
Whether you’ll soon be needing hydroforming services, are looking to leverage the benefits of pre-production Finite Element Analysis (FEA) for your product prototype, or are just shopping around becau …

What is Tube Hydroforming: an Explanation of an Important Procedure
Overview of Tube Hydroforming
Tube hydroforming is one of two groups within the broader category of hydroforming itself, along with sheet hydroforming. It is a relatively new manufacturing process, …
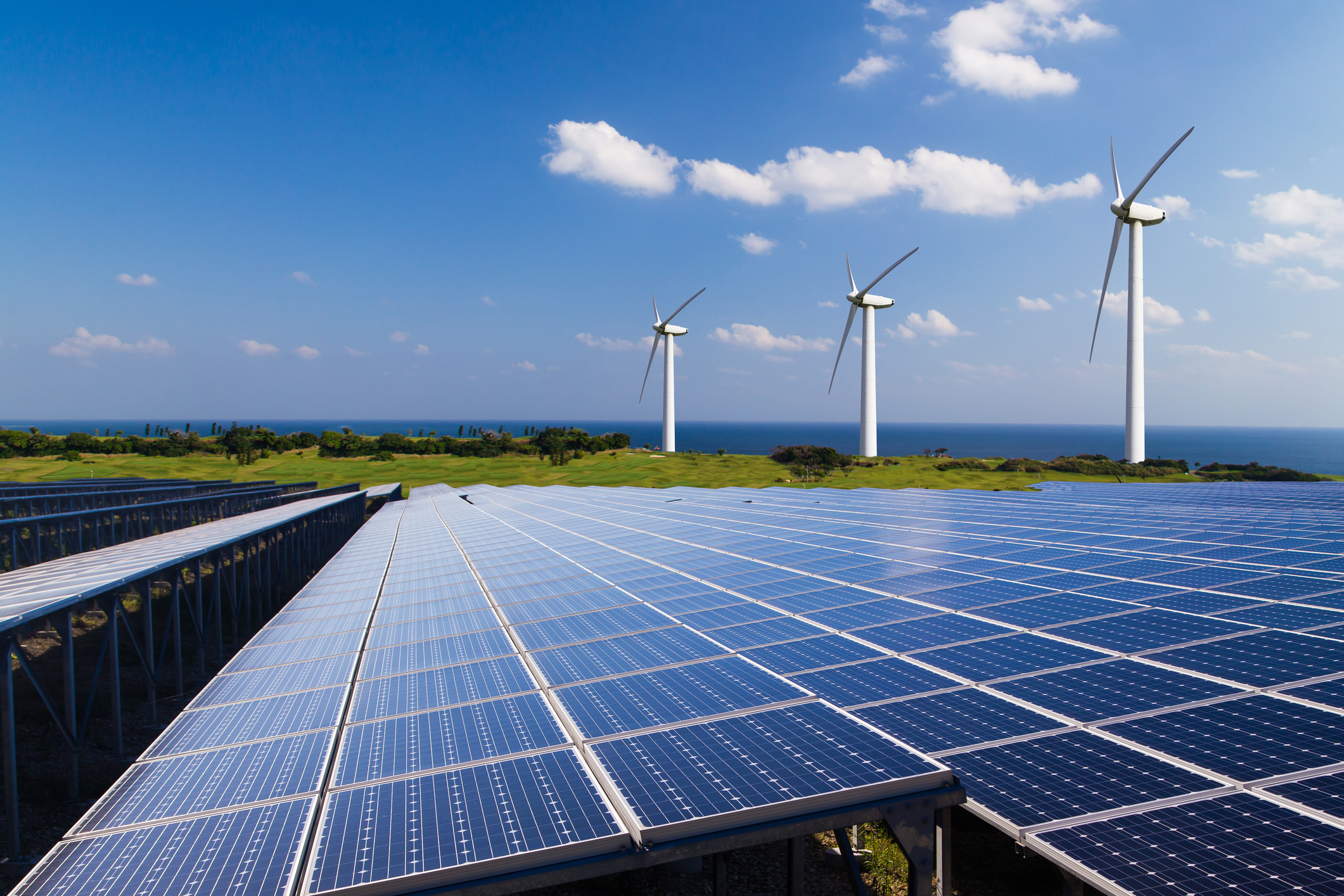
American Hydroformers: The advantages of deep draw hydroforming
If you need a lightweight metal part with a depth larger than the radius, deep draw hydroforming is the way to go. This versatile process makes lightweight, durable parts that are deeper and more accu …

Say Hello to the Midwest Hydroforming Masters: American Hydroformers
Many people think of the Midwest as the American Heartland. They assume that everyone here is corn-fed, home-grown, and hearty. Honestly, if this is your opinion, we don’t hold it against you. History …

Making Finite Element Analysis Work for You
Adding an extra step to a process is rarely considered efficient. After all, streamlining steps usually means that tasks are accomplished more quickly. However, if the added step is designed to save t …

What is Tube Hydroforming: A Step-by-Step Guide
Tube Hydroforming, a metal fabricating and forming process, helps to shape metals into their desired shapes. This technique can be used to shape various metals including steel, aluminum, brass, copper …

American Hydroformers: The Midwest’s Hydroforming Experts
If you are in or around the Midwest and in need of some hydroforming, we suggest that you give us a try. American Hydroformers is the Midwest’s top hydroforming company, and we can give you three reas …