
Hydroformed Parts Key to Meeting CAFE Standards
Corporate Average Fuel Economy (CAFE) standards regulate the fuel economy of vehicles sold in the United States. Rather than requiring minimum fuel efficiency standards for each vehicle, CAFE requires …
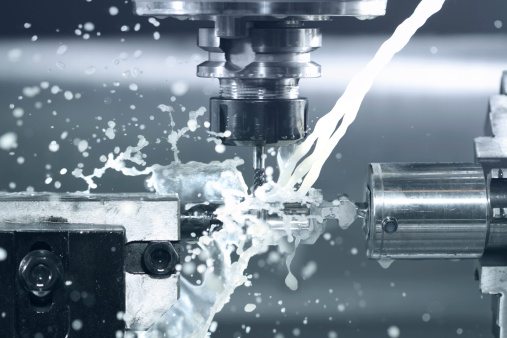
Do You Have A Process Control System For Your Metal Stamping Production?
When you can control your manufacturing process, you will have a better chance of increasing your production, improving your quality, and reducing the overall costs. You need to have the right indicat …

Though Struggles Exist, Hydroforming and Metal Stamping Thrive
U.S. manufacturing in the new tech age has brought with it many advances for those involved in the industries of metal stamping and hydroforming. However, at the same time, it has cont ...

Tubular Hydroforming And Other Innovative Techniques
Whenever you are working on a project, no matter how big or how small, you should always look for the best possible way to make the project successful. When you want the project done correctly, it doe ...

2016 CAFE Standards: What the Near Future Holds
Beginning in 2011, automobile makers had to meet a set of government regulations that had sat in limbo for many years. For many, this was the biggest change in fuel-economy standards since the 1970s C ...

3 of the Latest Hydroformed Components Hitting the Market
As we so often do, we like to focus on hydroformed components that are making waves in the modern world. From mountain bikes to car parts to aerospace design, hydroformed components and prod ...
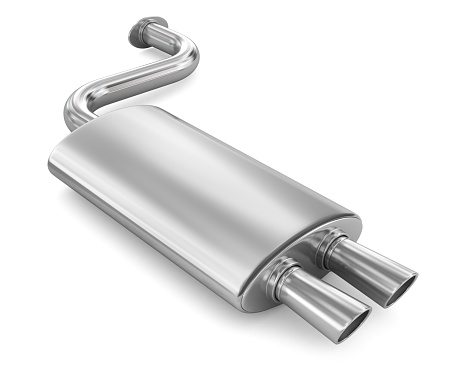
5 Benefits of Hydroformed Components
In the middle of the US, located in what is universally known as the "breadbasket" of America, sits the heart of hydroforming in the Midwest. The sometimes seldom-known but vastly innovative productio ...

How Hydroformed Components Make Products Better
Hydroformed components and hydroforming positively impact how manufacturers produce. After all, hydroforming adapts to needs and makes lighter, more durable, and longer-lasting products, which benefi ...

The Benefits Of Hydroforming
The process of hydroforming has been kicked around the manufacturing industry for quite some time. The process involves forming ductile metals such as stainless steel, aluminum, brass, and low allow s ...
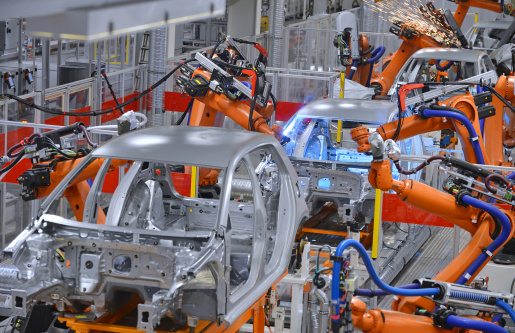
Hydroformed Components Make Trucks Stronger, Faster, and Better
We've talked in length before about how hydroformed components used in the automobile industry have helped to change the entire process. Every few months or so, we like to update our reader ...