
Hydroformed Parts Key to Meeting CAFE Standards
Corporate Average Fuel Economy (CAFE) standards regulate the fuel economy of vehicles sold in the United States. Rather than requiring minimum fuel efficiency standards for each vehicle, CAFE requires …
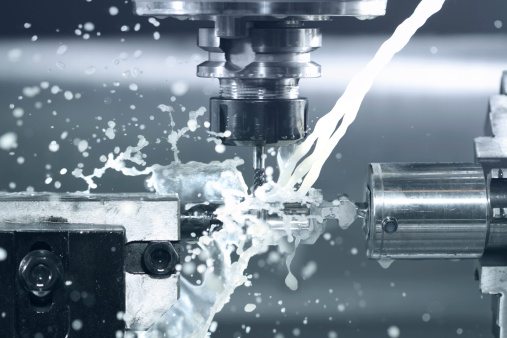
Do You Have A Process Control System For Your Metal Stamping Production?
When you can control your manufacturing process, you will have a better chance of increasing your production, improving your quality, and reducing the overall costs. You need to have the right indicat …

How Tube Hydroforming Can Help Cafe Standards?
CAFE Standards: The Corporate Average Fuel Economy standards (CAFE) standard enacted in 2014 imposes fuel efficiency and green house gas emission standards on the manufacturers of cars and medium a ...

Tubular Hydroforming And Other Innovative Techniques
Whenever you are working on a project, no matter how big or how small, you should always look for the best possible way to make the project successful. When you want the project done correctly, it doe ...

Hydroforming Aluminum Vs Stamped Steel
The rise of hydroforming as a viable manufacturing process which reduces the weight of resulting items is driving two distinct transitions in the industry. One of these is the switching from stamping ...
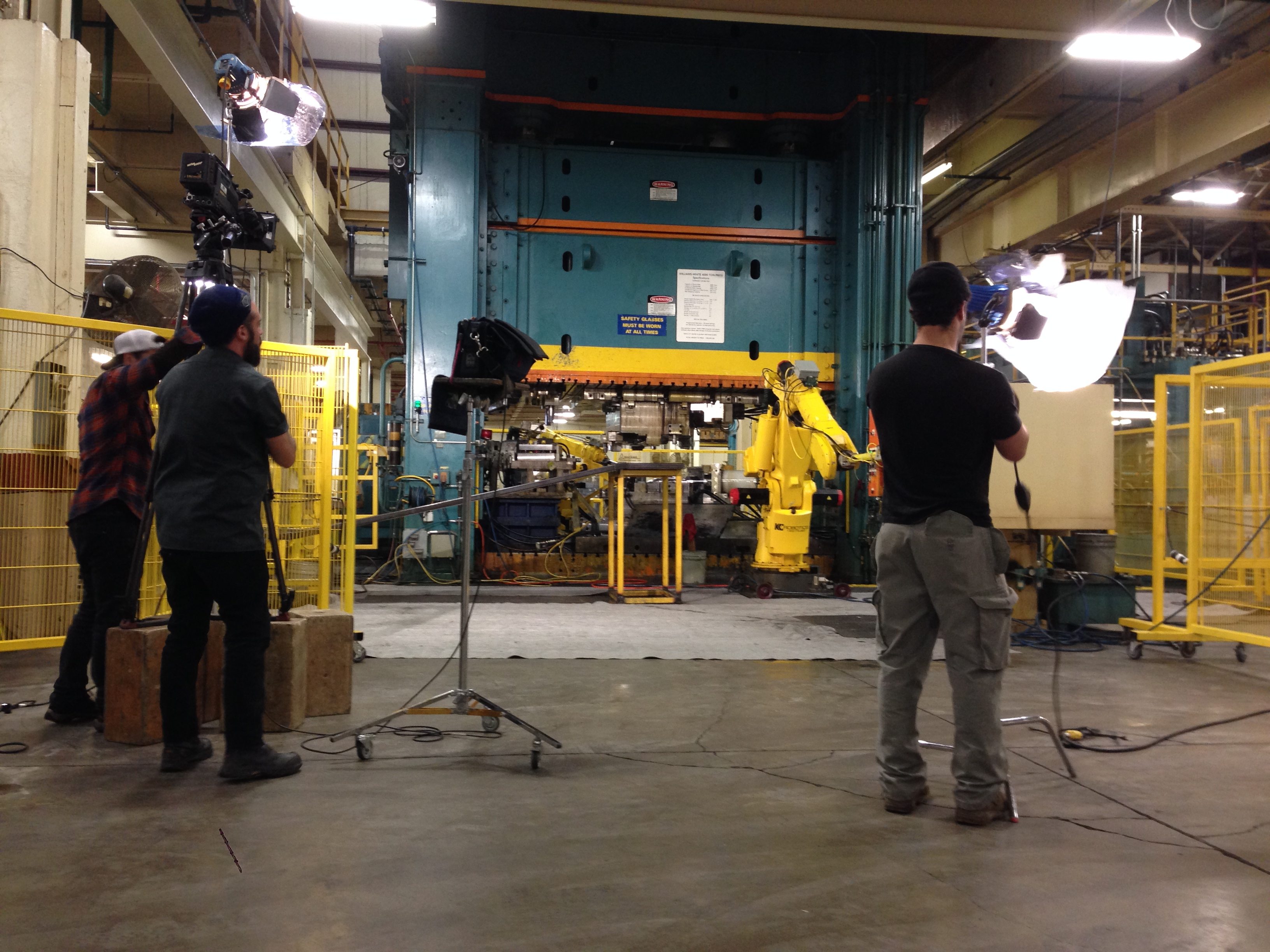
American Hydroformers, Inc. to be Featured on the Science Channel/Discovery Channel’s “How It’s Made” Television Program.
SUMMARY: American Hydroformers is proud to announce that the company will be featured on a segment of the Science Channel/Discovery Channel’s popular “How It’s Made” television program. This detailed ...
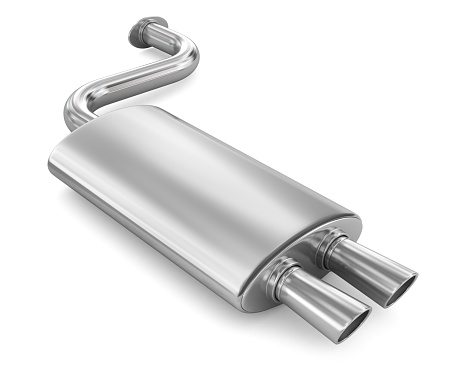
5 Benefits of Hydroformed Components
In the middle of the US, located in what is universally known as the "breadbasket" of America, sits the heart of hydroforming in the Midwest. The sometimes seldom-known but vastly innovative productio ...

How Hydroformed Components Make Products Better
Hydroformed components and hydroforming positively impact how manufacturers produce. After all, hydroforming adapts to needs and makes lighter, more durable, and longer-lasting products, which benefi ...
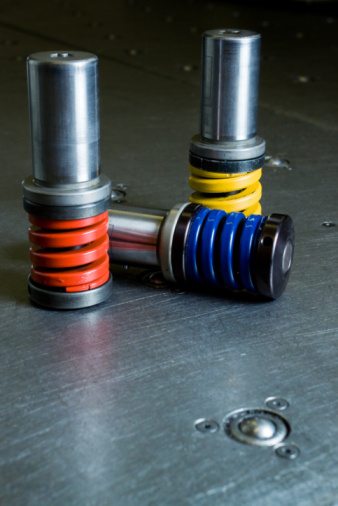
Report Says: Metal Stamping to Increase Thanks to Auto Industry
Metal stamping is a very important process to the manufacturing of automobiles. It plays host and is integral to a broad range of parts and finished goods. It transforms flat sheets of metal into ...

The Budding New Technique of Friction Stir Welding
A relatively young technique in the field of welding, friction stir welding was invented then scientifically proven as a viable method in December of 1991. By definition it is a 'solid-state joining p ...